2024.07.19 (Fri)
ビジネスを成功に導く極意(第66回)
AIによる検品自動化の裏に試練あり。大手プロセスチーズメーカーの挑戦
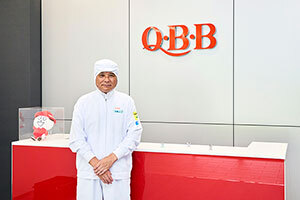
「QBB」のブランドで知られる六甲バター社は、主力製品のベビーチーズにおける検査工程を、AIにより自動化しました。しかしその過程には、さまざまなトラブルが存在しました。
目次
QBBブランドのチーズは、AIが検査をしている
「QBB」というアルファベット3文字を聞くと、おそらく多くの人が「チーズ」を思い浮かべることでしょう。
QBBは、六甲バター株式会社が手がけるチーズのブランドです。同社は1948年に「平和油脂工業株式会社」として創業し、当初はマーガリンを製造していましたが、1958年よりプロセスチーズの生産をスタート。以降、QBBのブランドでチーズの販売を続けています。
QBBとは「Quality's Best & Beautiful」の頭文字を取ったもので、「安全についての妥協を排除し、だれもが安心して食べられる健康的な製品の提供」という、同社のチーズの品質に対するこだわりがそのままブランド名に反映されています。現在QBBのチーズは、家庭用や学校給食用、業務用を含めて約300種類もの品揃えが存在し、特にチーズを個包装にした「ベビーチーズ」は、年間2億本を超える人気商品となっています。
そんな同社は2019年、チーズの生産体制の強化のため、神戸市西区に「神戸工場」を新設。同工場では生産の効率化と省人化のために、AIで検査工程の自動化をスタートさせます。
しかし、実際にAIを生産過程に組み込むためには、いくつかの困難があったといいます。同社はどのようにしてAIを導入し、それによってどのような効果が得られたのでしょうか?同社の執行役員 神戸生産部長の小泉忠氏に、プロジェクトの過程を聞きました。
チーズの検品を、人間ではなくAIに任せる理由とは
六甲バターの本社は神戸市中央区の市街地に存在しますが、2019年に竣工した主力製造所である神戸工場は、本社から西に10km以上離れた、自然に囲まれた山間地に存在します。
小泉氏は同工場の設計コンセプトの1つに、主力製品であるチーズの生産性を大幅に向上させることがあったと話します。
「神戸工場では、家庭用・業務用など約300品目の製品を製造しています。中でもベビーチーズについては、生産装置も最新のものを導入しており、チーズの重量調整や、包装ロスの除去など、自動化が可能な部分はできるだけ自動化し、業務が省人化できるような取り組みを進めてきました」(小泉氏)
神戸工場では業務効率化のため、従来は目視で行っていたベビーチーズの外観の検査を、AIによって省人化することも計画されていました。
「従来のベビーチーズの製造工程では、チーズの充填機の出口で、検査員が目視で検査していました。検査員は4列で流れてくるチーズを目視でチェックし、不良品があれば取り除くという作業を担当していましたが、1分間で500個ものチーズを目視しているため、これを長時間見続けて判断する作業は大変なことです。常に集中力を保つ必要がありますし、検査員の熟練度によって、検品の性能が左右されることもあります。
これまでは20人以上の検査員が交替制で担当していました。
たとえ優秀な検査員であっても、調子が悪い日は当然あります。この作業を自動化し、より検品の精度を高めることは、生産性を高める点でもメリットは大きいと考えました」
そこで同社は、AIによる製品外観検査装置の開発に着手することを決定。パートナーである清水建設とタッグを組み、神戸工場の完成に先駆けた2016年より開発をスタートしました。
チーズが柔らかすぎて、AIが学習できない?
開発の分担としては、まずは六甲バター社が検査装置のアイデアを作成し、AIに学習させる画像データを清水建設に提供。それらを元に清水建設が、AI装置のハードウェアとAI検査システムを作成するというものでした。
両社が計画したAIによる検査装置は、1レーンにカメラを2台設置し、個包装状態のベビーチーズの底面以外の5面をカメラで撮影、その画像をAIがチェックすることで、製品の良否を判定します。プロジェクトを始めるにあたって、AI検査装置が不良品を発見する精度を、検査員の目視検査と同程度とすることにしました。
しかし、この装置を開発するにあたっては、いくつもの壁があったといいます。 「まずはAIに、何が良品なのか不良品なのかを学習させるデータ取得のため、検査場にカメラを据え付け、良品/不良品の画像データを収集することからスタートしました。検査員が不良品を発見した際には、検査装置のスイッチを操作することで、画像データに『NG品』というデータラベルを付けます。
とはいえ、ベビーチーズは大量に作られるため、NG品を発見した場合、検査員は速やかにスイッチを操作しラベル付けを行う必要があります。担当者は相当な苦労をしながら、ラベル付けの作業を行っていたことをよく覚えています」
検査員が急いで良/否の判定を行わなければいけない背景には、ベビーチーズならでは理由がありました。
「充填されたばかりのベビーチーズは高温で非常に軟らかく、手で取り扱うときでも、形状がすぐに変わってしまいます。そのため、生産ラインで検査員がNG品として判定したチーズを、手でやさしくつかみ、生産ラインから取り出した後、チーズの形状を撮影しても、それは本来のNG品の形状とは異なるため、参考にはなりません。NG品のデータを集めるためには、ラインから排出される前の画像を撮影し、急いでラベルを付けるしか方法がありませんでした。
さらにいえば、何をもってNG品とするか、その基準が検査員によって微妙に異なっていることもありました。基準がそろっていなければ、AIも正確に判断できません。まずは品質基準を標準化し、“基準値から何ミリずれるとNG”といったような、明確な基準を定めることもしました」
これ以外にも、画像の撮影方法や、画像をAIに学習させるタイミングでも、さまざまなトラブルが発生したといいます。
「ベビーチーズにはアルミ包装材が使われていますが、その光沢によって光が反射したり、影ができることで、AIの学習にも悪影響が出てしまいました。その影響を抑えようと、当初はモノクロカメラを採用していました。モノクロカメラは微妙な光沢や影の違いを捉えるには効果がありましたが、包材を剥く際に使用する赤色フィルムの良否判定には向いておらず、色情報を使って判別させるため、カラーカメラに変更することにしました」
このように機材を入れ替える度に、学習用のデータセットも作り直す必要があります。カメラのレンズを変更したこともありましたが、その際にもデータセットを作り変える作業が発生しました。
さらに、プロジェクトスケジュールが延びたことで、使用していたパーツが入手できなくなったり、バージョンアップしたことで、プログラムが動作しなくなり、新しいパーツやバージョンに合わせたアップデートが完了するまでプロジェクトが停滞するトラブルが何度も発生しました」
AI検品で検査員を1/4に削減。当該スタッフはより高度な業務へ
こうしたいくつもの課題を乗り越え、六甲バター社のAIによる画像検査装置は、2022年10月の省人化達成を皮切りに、横展開が進んでいます。
「神戸工場には複数台の生産装置がありますが、うち1号機は、ようやく2022年10月に目標となるNG品の確実な排出と歩留りを達成できました。さらに2022年12月には、2号機でも省人化も達成。その後、電装部品が入手できない困難な時期もありましたが、2023年8月には3号機でもAIによる省人化が実現しました。
この2024年4月には、残りの検査装置の搬入と据付が完了し、完成に向けた次のデータ収集に入ったところです。AI学習モデルで自動判別することで、重要な欠陥品が、検査員の目視なしで排出できる。この効果は大きいです」
同工場では検査業務の省人化により、目視確認など検査工程を担当する検査員の数が、従来の約4分の1にまで削減できるといいます。現在、かつて検査員だったスタッフは、機械・機器の運転や調整業務を学び、それらの機器のオペレーター補助として、スキルを大幅に上げているといいます。
「元検査員のスタッフは、機械の状態をよく理解しています。そのため、AIで不良判定が増加した際にも、装置の不具合にいち早く気付き、点検・調整を行う体制が構築できます」
「何がOKでNGか」の基準は、社内で苦労して作るべきである
小泉氏は今回のプロジェクトを振り返り、AIによる検査体制が築けた要因として、何を持って良/否とするか、その判断基準となる学習用データセットに加え、学習モデルを、社内で調達した点にあったと分析します。
「今回のプロジェクトでは、AIが良品か否かの判断に使用する画像データを、現場責任者が用意しました。作業は大変でしたが、結果的にNG品への確実な反応と歩留りを両立できる精度の高い学習データセットができあがりました。AIが判断をするうえで基準となるデータは、結局は人間が作り込む必要があります。何がOKで何がNGなのか、その基準を正しく判断すべき人が、多大な労力を使って学習用データセットを用意したことが、良い結果に結びついたと考えています。
弊社を含め多くの企業には、品質を高く維持する部門が組織化されています。今回のAIによる検査工程の実装は、品質保証の観点から判断しており、AIが、我々が生産するチーズの品質を高いままで維持していると、自信を持っています」
同社では今後のAI活用について、検査だけで無く、他の工程にも導入できるよう検討しています。
「現在検討しているのが、生産機器の劣化具合を検知し、部品の交換や修理のタイミングを予測する『予知保全』にも、AIを活用したいと考えています。工場で使用する生産機器は、当然ながら使い続ければ続けるほど劣化し、最悪の場合は故障に至ります。そうなれば、チーズの生産も難しくなり、商品を市場に送り出すことも難しいです。一方で、故障を恐れるあまり頻繁にメンテナンスを行うと、今度は稼働時間が短くなり、非効率です。
しかし、AIが生産機器の状態を検知し、適切にメンテナンスのタイミングを知らせることができれば、現在よりも効率の良い生産体制を構築することが可能です。もちろん簡単なことではありませんが、神戸工場は効率化と省人化のために設立された工場です。これから取り組む価値はあると考えています。
QBBブランドのQとは「クオリティ」のことですが、チーズに対するクオリティはもちろん、チーズを製造する生産機器にも、引き続きこだわっていきたいと考えています」
ベビーチーズブランドサイトはこちら
まるっと解説、「工場(OT)セキュリティ」の課題から対応まで
連載記事一覧
- 第1回 劇的な変化をみせるネットスーパーが目指すもの 2016.04.12 (Tue)
- 第2回 家電メーカー「アクア」を成功に導いた風雲児 2016.04.19 (Tue)
- 第3回 下町ロケットを例に考える、競合に打ち勝つ戦略 2016.06.21 (Tue)
- 第4回 ロート製薬の副業解禁は朗報か悲報か? 2016.06.28 (Tue)
- 第5回 広島オバマ演説に見る最高の「問いかけ」手法 2016.07.13 (Wed)
- 第6回 「運が良い人」「運が悪い人」の違いはどこにある? 2016.10.13 (Thu)
- 第7回 非正規→正規雇用で助成金、経営に役立つ制度7選 2016.10.25 (Tue)
- 第8回 会話上手な人になるための3つのポイント 2016.11.17 (Thu)
- 第10回 手帳は「目盛り」があるものを選んだ方が良い!? 2017.02.17 (Fri)
- 第11回 中小企業必見、銀行の「融資姿勢」を知る指標がある 2017.03.09 (Thu)
- 第12回 辛いときこそ「ポジティブシンキング」すべき理由 2017.03.16 (Thu)
- 第13回 「宅配便ロッカー」に見る、人手不足問題の解決法 2017.04.17 (Mon)
- 第14回 どうしてGoogleはメールを使わなくなったのか!? 2017.06.15 (Thu)
- 第15回 たった5日間で難解な課題も解決するGoogleの仕事術 2017.08.04 (Fri)
- 第16回 企業の業務改善を実現する、いま話題の「BPM」とは 2017.08.08 (Tue)
- 第17回 サイバーエージェント流、社員の強みを伸ばす方法 2017.09.08 (Fri)
- 第18回 会議を無駄な時間としないための、3つのポイント 2017.10.11 (Wed)
- 第19回 あなたのToDoリストの作り方、間違っているかも!? 2017.10.18 (Wed)
- 第20回 美意識の向上が経営力のアップに!? 2017.11.20 (Mon)
- 第21回 タスク管理がはかどる手帳術「バレットジャーナル」 2017.12.14 (Thu)
- 第22回 中国が欲する日本サッカー育成術とビジネスの共通点 2017.12.26 (Tue)
- 第23回 アイディアが整理され、企画案がまとめやすいメモ術 2018.01.18 (Thu)
- 第24回 キャッシュレス化は後進国の国内カード事情 2018.02.20 (Tue)
- 第25回 3密必至の接客業にニューノーマルビジネスを学ぶ 2020.06.26 (Fri)
- 第26回 日本全国で初めて迎える“マスク × 夏 × 作業現場” 2020.06.26 (Fri)
- 第27回 仕事がスイスイ片付く「テレワーク時間管理術」 2020.09.29 (Tue)
- 第28回 ビジネスパーソンに不可欠、よい短文を書くコツ 2020.10.06 (Tue)
- 第29回 デキる人は実践済み、レポート・報告書作成のコツ 2020.10.06 (Tue)
- 第30回 デキる社会人は、なぜビジネス手帳を使うのか 2021.02.19 (Fri)
- 第31回 「伝わる」プレゼン資料作成5つの鉄則 2021.03.09 (Tue)
- 第32回 絶対に知りたい、副業をはじめる際のポイント 2021.03.09 (Tue)
- 第33回 それ、間違いかも!? 戸惑いがちなビジネスマナー 2021.03.12 (Fri)
- 第34回 日本に必要なのは「問題児」。APU出口学長が語る 2021.04.19 (Mon)
- 第35回 好感を与えるメール署名の書き方 2021.05.31 (Mon)
- 第36回 建設の人手不足を解消する、子ども向けキャリア教育 2021.06.03 (Thu)
- 第37回 職人・工場をつなぐ製造業ビジネスマッチングサイト 2021.06.03 (Thu)
- 第39回 「かかりつけ薬剤師」に指名されるための3つの方法 2021.06.15 (Tue)
- 第40回 かっぱ寿司やパルコも導入「サービスロボット」とは 2021.06.15 (Tue)
- 第41回 「もうすぐ故障」がわかる、故障予知技術のいま 2021.06.15 (Tue)
- 第42回 ウェブ会議をうまく仕切る人がやっていること 2021.06.15 (Tue)
- 第43回 コロナ禍で明暗を分ける"与える営業"と"もらう営業"2021.06.23 (Wed)
- 第44回 ワークマンを支える「Excel経営」とは?土屋専務に聞く 2021.09.07 (Tue)
- 第45回 レトロブームにみる若手社会人の新しく古い価値観 2021.09.14 (Tue)
- 第46回 大手や中小企業も活用、BtoBマッチングサービスとは 2021.09.14 (Tue)
- 第47回 コロナ禍でも、実店舗で売上をUPする方法がある 2021.09.28 (Tue)
- 第48回 スポーツ分析官が語る、組織が成長するデータ活用術 2021.09.30 (Thu)
- 第49回 「ディフェンス重視」が、生き残る企業の条件になる 2022.06.27 (Mon)
- 第50回 ビジネス拡大の可能性を秘めた「サステナブル・シーフード」とは2023.04.28 (Fri)
- 第51回 大谷選手のCMが証明した、ジェンダーレス市場ECの勝算2023.04.28 (Fri)
- 第52回 なぜ音声コンテンツはZ世代の心を掴むのか2023.05.30 (Tue)
- 第53回 バーチャル・トライオンとは?事例を交えて紹介2023.07.05 (Wed)
- 第54回 半数以上の企業が副業・兼業を支持、ワーキッシュアクトの可能性を探る2023.07.05 (Wed)
- 第56回 挑戦がブランドになる。財政難バスケチームの逆転劇2023.11.22 (Wed)
- 第57回 2億円の売上増↑山形の製造業はDXで何を変えたのか2023.11.22 (Wed)
- 第58回 なぜ大谷翔平は、野球と関係の薄い企業の広告に起用されるのか?2024.03.01 (Fri)
- 第62回 市民と行政の間の溝を「シビックテック」が埋める2024.03.29 (Fri)
- 第62回 モノを売らない店舗「ショールーミングストア」の可能性2024.03.29 (Fri)
- 第60回 万博で話題の「空飛ぶクルマ」ってどんなクルマ?2024.03.29 (Fri)
- 第61回 高円寺の老舗銭湯が挑む「あえて無駄を残す」DX 2024.03.29 (Fri)
- 第64回 なぜウォーキングすると、ポイントが付与されるのか?2024.07.11 (Thu)
- 第65回 なぜメタバースが「不登校」の支援に使われているのか2024.07.11 (Thu)
- 第66回 AIによる検品自動化の裏に試練あり。大手プロセスチーズメーカーの挑戦2024.07.19 (Fri)
- 第67回 顧客の判断力を低下させる「ダークパターン」にご注意2024.08.08 (Thu)
- 第68回 すでに教育の現場で導入済み。生成AIを"教材"として使う方法2024.08.13 (Tue)
- 第69回 熱中症から作業員を守る最新ソリューションとは2024.08.13 (Tue)
- 第70回 クールビズを脱炭素に繋げる「デコ活」がスタート2024.09.24 (Tue)
- 第71回 中古なのに新品!?エコな商品「リファービッシュ」とは2024.10.08 (Tue)
- 第72回 文具店がDX支援企業にチェンジ!華麗な転身を遂げた宮城県の企業に迫る2024.10.09 (Wed)
- 第73回 捨てればゴミ、回収すれば資源。「電子ごみ」の正しい捨て方2024.12.27 (Fri)
- 第74回 開始1年半で1,000社突破!非ITの老舗製造業が始めたクラウドサービスとは2025.01.30 (Thu)