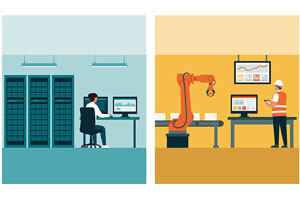
人手不足や生産性向上といった日本が抱える課題への有効な対策の一つがDX化です。しかし、製造業において本質的なDX化を進めるためには、OTシステム(Operation Technology/制御・運用技術)と、ITシステム(Information Technology/情報技術)の融合を実現しなければなりません。本記事では、OTとITが分離しがちな理由と、融合のために必要なことについて解説します。
OT・ITの違い、融合するメリットとは?
OTとは、工場や発電所などの設備を動かすための制御・運用技術の総称です。製品を作るためのロボットやセンサーを動かしているのがOTです。一方ITとは、情報通信技術やコンピューター技術の総称です。具体的には、企業が使用しているソフトウェア(基幹システムなど)やハードウェア(サーバやPCなど)、通信網(Wi-Fiなど)などを指します。
これまでOTはインターネットに接続せず、工場や発電所などの閉じられた環境で稼働することがほとんどでした。しかし、ITと融合することで生産設備の情報が自動的に収集できるなど、さまざまなメリットが生まれます。
・データドリブンな意思決定
生産部門や品質管理部門では、情報を迅速に把握できることで改善策の立案や意思決定スピードと精度の向上が見込めます。さらに、現場担当者は日報などの入力・報告業務の工数を削減できます。従って、データドリブンな経営戦略・経営判断を行うことが可能になるでしょう。
・データ分析による生産性向上
たとえば、生産データに基づいて人員配置を見直すことで、生産性の改善やコスト削減につながる可能性があります。ほかにも、品質管理レベルの高度化を図り、安全・安心な生産現場をつくったり、生産現場のデータを踏まえて、サプライチェーンの在り方を考えることで、今以上に利益を確保しながら、顧客の需要にきちんと応えていくこともできるかもしれません。
・CO2の排出抑制にも活用
2050年カーボンニュートラルの実現に向けて、企業は事業活動におけるCO2排出量を把握し、CO2排出削減に取り組む責任があります。CO2排出を削減するためには、企業活動全体の排出量を把握する必要があります。ある日本企業では、CO2排出量を見える化し、経営と連動させるなど、すでにOTとITを融合させ脱炭素経営を進めているケースも存在しています。
人間、機械、その他の経営資源が互いに通信することで、仕入・製造から納品までの情報を共有し、製造プロセスをより円滑にします。インダストリー4.0を実現する動きの中でも、OTとITの融合が求められますが、分離したままでは先述のメリットを享受できないだけではなく、企業の競争力が低下するリスクも考えられます。ある調査によれば、OTがITシステムに接続されている企業は50%程度とも言われており、まだまだ融合が進んでいないのが実情です。
なぜか進まないIT・OT間のデータ管理や一元管理
OTとITの融合が進まない原因はいろいろありますが、主な原因の一つは、OTとITの管理主体が別組織であることです。OTとITは別の事業体のものとして組織された上に、サイロ型の組織構造になっているケースがあります。
また、OTは情報システム部門を介さないシステム構築が行われ、ITと統合管理されていないことがあります。IT管理者がOTについて十分に理解できていなかったり、OTセキュリティを管理する部門・担当が存在しないケースもあります。さらに、IT部門はデータの安全性とセキュリティを重視し、OT部門は生産性、安全性、稼働率を重視するという文化の違いも融合が進まない理由の一つでしょう。
他にも、レガシーシステムであることが多いOTと日々進化を続けるITを融合させるためには、技術的に高いハードルがあります。通信方法が異なるケースもあるので、融合させるためには、適切なソリューションが必要です。しかし、進化し続けるITと信頼性を重視するOT双方に精通した人材はほとんどおらず、運用ノウハウもないため、融合させることは容易ではありません。
セキュリティ面では、これまでクローズド環境で運用されていたOTがネットワークにつながることで、新たな脆弱性が生じる可能性があります。OTがサイバー攻撃を受けた場合、工場の稼働が停止してしまい、サプライチェーン全体に大きな影響を及ぼします。こうしたリスクも、OTとITの融合になかなか踏み出せない要因となっています。
OTとITの融合を進めるために必要なこととは?
OTとITの融合を進めるためには、管理者(責任者)を統合するか、緊密な連携を取ることが重要です。IT管理者がOTについて理解し、工場の機器や外部との接続など、基本的な構成や環境を把握することが不可欠です。
特に、セキュリティ対策を施す上では、製造現場のネットワーク環境を確認することは欠かせません。機器名やベンダー名、インストールされているOSやソフトウェア、ネットワーク構成、通信トラフィックなども可視化しておくことで、脆弱性のリスクを把握できます。技術的な問題は、専門企業の支援を受けながらセキュリティアセスメントを実施してみましょう。加えて、OTとITのセキュリティの違いを理解することも必要です。OTでは、工場が止まって損害が出るのを防ぐため、システムや情報をいつでも使える「可用性」が、ITでは、情報漏洩を防ぐため「機密性」が最優先されます。
OT部門とIT部門の連携が充分ではない場合、万が一の場合に対応できるように、セキュリティ対策は運用しやすいようにシンプルな構成を考える必要があります。合わせて対応方法などのフローが分かる、セキュリティガイドラインの作成も必要です。
前述したインダストリー4.0の主眼は、スマートファクトリーを中心としたエコシステムの構築です。ITとOTの垣根をなくし、人間や機械、その他の経営資源のすべてがネットワークを介して接続されることで、各製品の製造時期や納品先を瞬時に把握し製造プロセスを円滑化、既存のバリューチェーンの変革など、新たなビジネスモデルの構築をもたらすことが期待されています。
OTとITの融合は、生産現場の効率化や省力化といったことにとどまらず、モノづくりの競争力を高めるための大きなテーマです。専門的なスキルとノウハウを持った外部企業のサポートも受けながら、取り組みを進めていきましょう。
連載記事一覧
- 第1回 製造業におけるDX(デジタルトランスフォーメーション)の必要性とは?事例も合わせて紹介 2022.03.04 (Fri)
- 第2回 製造業における機械学習の事例および活用可能な機械学習技術について解説 2022.03.04 (Fri)
- 第3回 工場のスマートファクトリー化を進める課題とは何か 2022.03.04 (Fri)
- 第4回 ローカル5Gとは? 工場で導入する方法や事例を解説 2022.03.04 (Fri)
- 第5回 ファクトリーオートメーション(工場の自動化)とは?今後はどうなる? 2022.03.04 (Fri)
- 第6回 スマートファクトリーの土台となる工場のネットワークとは? 2022.03.04 (Fri)
- 第7回 ファクトリーオートメーションの事例や企業、今後とは? 2022.03.04 (Fri)
- 第8回 2021年6月より義務化! 食品事業者が知っておくべきHACCPの基本と事例を紹介 2022.03.04 (Fri)
- 第9回 製造業で注目を集めている「Anywhere Operations」とは?概要などについて解説 2022.03.04 (Fri)
- 第10回 製造業における情報セキュリティリスクの高まりとその対策方法 2022.03.04 (Fri)
- 第11回 製品開発のDX化のカギを握るCAE解析とは? 2022.03.04 (Fri)
- 第12回 製造業で導入が始まっているデジタルツインとは 2022.03.04 (Fri)
- 第13回 インダストリー4.0とは?概要や課題、事例などを紹介 2022.03.04 (Fri)
- 第14回 製造プロセスの最適化が期待できるPLMソリューションとは 2022.03.04 (Fri)
- 第16回 製造業を取り巻く現状と考えられる課題とは? その対策についても解説2023.01.30 (Mon)
- 第18回 工場を見える化するには? メリットや具体的な方法を紹介2023.01.30 (Mon)
- 第19回 製造業におけるヒューマンエラー対策とは? エラーが起こる原因も解説2023.01.30 (Mon)
- 第25回 製造業の今後は? 現状の課題や生き残るための手段を解説2023.01.30 (Mon)
- 第42回 事例から学ぶ、被害最大の「製造業」ランサムウェア対応2024.03.29 (Fri)
- 第43回 【用語解説】製造業が必ず押さえたい3つのセキュリティトレンド2024.03.29 (Fri)
- 第44回 工場停止で数千万の損害も、製造業に"すぐ必要"なサイバー攻撃対策とリスクアセスメント診断2024.03.29 (Fri)
- 第45回 自社だけ万全でも意味がない、サプライチェーン攻撃を防ぐには2024.03.29 (Fri)
- 第46回 ITとの違いから学ぶ、OTセキュリティ強化で知るべきポイント2024.03.29 (Fri)
- 第20回 製造業における品質管理の重要性とは? 品質対策のポイントも解説2023.01.30 (Mon)
- 第47回 突然、取引停止?工場セキュリティ未対策のリスク2024.03.29 (Fri)
- 第48回 OTセキュリティ強化の必読書、経産省発行のガイドラインを読み解く2024.03.29 (Fri)
- 第49回 製造業にも遵守義務、EUサイバーレジリエンス法とは?2024.03.29 (Fri)
- 第50回 ゼロからはじめる工場のセキュリティ対策2024.03.29 (Fri)
- 第21回 トレーサビリティとは? 種類や製造業におけるメリットを解説2023.01.30 (Mon)
- 第23回 工場に求められる安全対策とは?その重要性と対策のポイントを紹介2023.01.30 (Mon)
- 第50回 OTとITの融合を進めるために考えるべきこととは?2024.08.09 (Fri)
- 第51回 ニーズを捉えるための「多品種少量生産」とは?2024.08.09 (Fri)
- 第27回 工場を見える化することで得られるメリットは? 具体的な導入の流れも解説2023.01.30 (Mon)
- 第28回 工場の省人化とは? 実現するための具体的な方法を解説2023.01.30 (Mon)
- 第31回 生産管理とは? 目的や内容からシステムの選び方までわかりやすく解説2023.01.30 (Mon)
- 第32回 製造業の生産性を向上させるメリットやその際の着目ポイントなどを解説2023.01.30 (Mon)
- 第30回 製造業で品質向上をめざすには? 解決すべき課題について解説2023.01.30 (Mon)
- 第33回 生産管理が属人化する理由とは? 解消方法と標準化するメリットを解説2023.01.30 (Mon)
- 第35回 製造業におけるコスト削減のポイントとは? 具体例や今後の動向を解説2023.01.30 (Mon)
- 第37回 製造業における働き方改革とは? メリットや成功のポイントを解説2023.01.30 (Mon)
- 第36回 SCMとは? メリット・デメリットやERPとの違いについて解説2023.01.30 (Mon)
- 第38回 【製造業向け】RPA導入のメリットや注意点とは?2023.01.30 (Mon)
- 第29回 工場にAIを導入するメリット・デメリット、失敗するケースを解説2023.01.30 (Mon)
- 第34回 QCDとは? 生産管理の考え方やQCDの改善法について解説2023.01.30 (Mon)
- 第15回 工場の改善アイデア・事例5選! 業務改善を成功させるコツや実施手順も紹介2023.01.30 (Mon)
- 第17回 製造業のヒヤリハット事例5選 報告書の書き方や対策の進め方2023.01.30 (Mon)
- 第22回 製造業にIoTを導入するメリットとは? 事例や課題を解説2023.01.30 (Mon)
- 第24回 生産管理はAIでどう変わる? 製造業におけるAIの活用事例を紹介2023.01.30 (Mon)
- 第26回 工場は深刻な人手不足。その原因と5つの対策法とは2023.01.30 (Mon)
- 第39回 増えている製造業へのサイバー攻撃! 理由や対策法を徹底解説2023.02.15 (Wed)
- 第40回 工場の現場をペーパーレス化するメリットとは? 導入ステップやツールを紹介2023.02.15 (Wed)
- 第41回 多能工化とは何か? メリット・デメリットと失敗しない進め方を解説2023.02.15 (Wed)