製造業でDXを実現するためには、デジタル技術の戦略的な活用が不可欠ですが、特に鍵を握るテクノロジーが「IoT」です。本記事では、IoTの基礎知識や製造業での活用事例、具体的な導入メリットなどについて解説します。
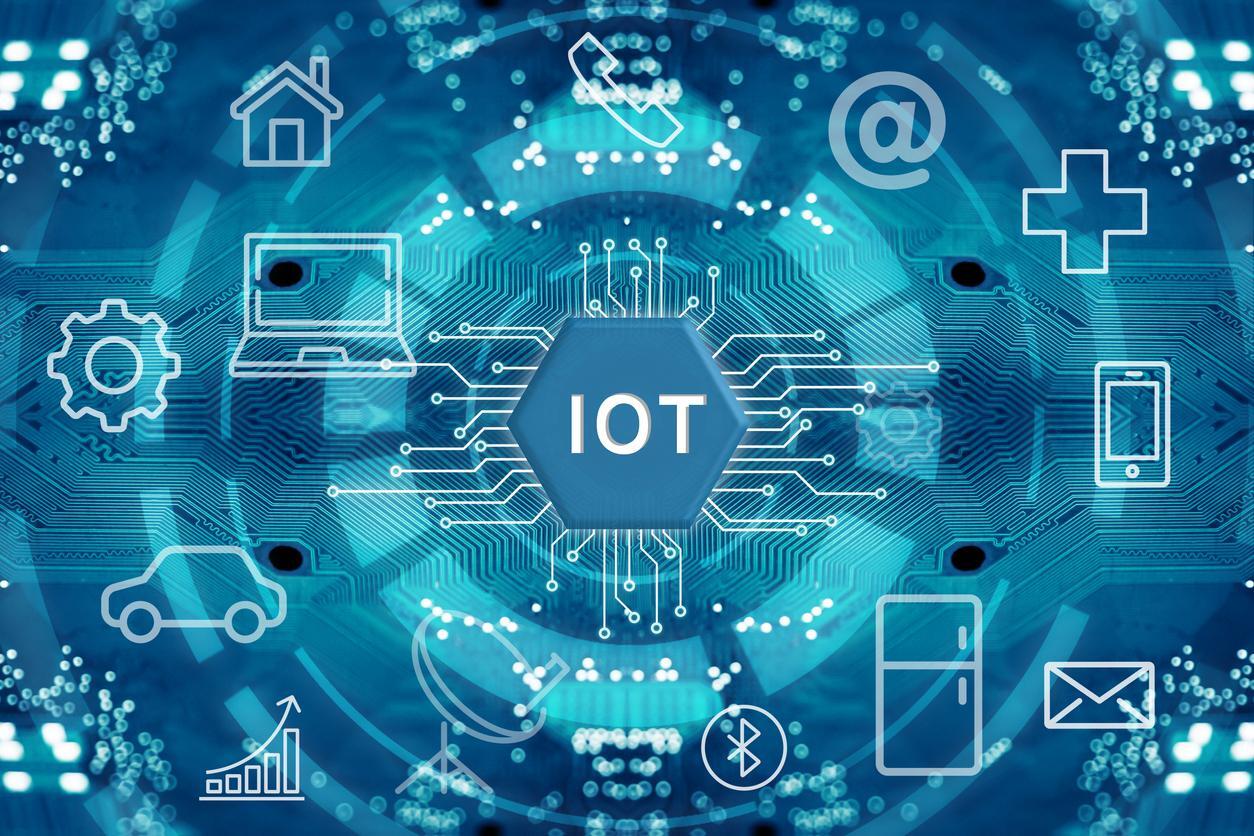
IoTとは
「IoT」とは「Internet of Things」の頭文字をとった略称で、さまざまなモノとインターネットを相互接続する技術のことです。IoTにはセンサーや無線通信が搭載されており、機器の状態など各種データを取得し、ネットワーク通信を介してコンピュータに伝送するのが、IoTの基本的な仕組みです。
IoTはすでにさまざまな製品に導入されており、たとえばスマートフォンでコントロールできる照明器具や、室温を自動で調整するサーモスタット、心拍数や睡眠の深さなどを測定するウェアラブルデバイスも、IoTに該当します。
IoTの基礎知識
製造業におけるIoTは、「スマートファクトリー」を実現するうえで欠かせないテクノロジーです。
スマートファクトリーとは、デジタル技術と生産設備や産業機器がネットワーク接続された先進的な工場を示します。工場内のあらゆる機器をネットワークに接続できれば、生産設備の稼働状況や製品の生産データなどの統合的な管理が可能となります。こうした先進的な生産体制を構築するには、工場内のデータを自動で収集・蓄積する仕組みが必要であり、その実現に欠かせないのがIoTなのです。
IoTでできること
IoTの核となる技術が、モノのさまざまな情報を取得・計測して数値化する「センシング技術」です。温度センサーや超音波センサー、感圧センサーなどのセンシング技術が搭載されたIoTを機器に取り付け、ネットワークに接続することで、機器のさまざまなデータが自動的に取得できます。
センシング技術によって可能となるのが、「モノの遠隔制御」「モノの状態を把握」「モノの動きを検知」「モノ同士での通信」という4つの領域です。
電子機器や工作機械を安定的に稼働させるためには、定期的な点検によって故障を防止する「予防保全」と、故障後に対応する「事後保全」の実施が不可欠であり、生産設備の保全業務に人材や資金を投入しなくてはなりませんが、スマートファクトリーを構築すれば、IoTが生産設備の稼働状況をリアルタイムに監視し、機器の異常を自動的に検知し、遠隔制御することが可能になります。生産設備の点検や巡回、監視業務などの省人化につながり、コストの大幅な削減や製造ラインの生産性向上に寄与します。
製造業におけるIoTの導入事例
実際に製造業において、IoTを導入した企業の事例を見てみましょう。
日本酒の製造および販売事業を展開する「合名会社寒梅酒造」では、代表の岩崎健弥氏が酒造りの一切を取り仕切る杜氏も兼任しており、経営者にとって最も重要なマネジメント業務に集中できないという課題を抱えていました。
この経営課題を解決すべく、同社はIoTを活用した遠隔での温度管理に挑戦。具体的には、酒蔵にIoTセンサーや温度計、カメラなどを設置し、タンク内の状況を遠隔地から管理できる生産体制を構築しました。計測されたデータはクラウド環境のストレージに蓄積され、時間や場所を問わずデバイスから情報を確認できる環境を整備することで、岩崎氏がマネジメントに集中できる経営体制の構築に成功しました。
製造業においてIoTを導入するメリット
IoTの導入が製造分野にもたらす代表的なメリットは、以下に挙げる5つです。
異常を素早く検知
製造分野の保全業務には、定期的な点検を行う予防保全と、故障後に対応する事後保全があります。生産設備のトラブルは製造ラインの停止につながるだけでなく、事故や怪我といった労働災害を招く要因となるため、ものづくり分野に携わる企業にとって予防保全と事後保全の精度向上は非常に重要な課題です。
IoTを導入すれば、生産設備の温度や作動音、動作速度、負荷などのデータが自動的に取得でき、エラーや故障も素早く検知できます。予防保全と事後保全の効率化や省人化につながるのはもちろん、保全業務の投じていた人的リソースの削減や労働災害の最小化に寄与します。
生産管理を自動化
製造業では、受注や製造の状況を把握しながら、部材の調達や製造工程、人材の配置などを、生産計画に基づいて適切に管理する必要があります。もし生産管理に不備があれば、原材料や部材の手配漏れが生じたり、工程進捗が把握できず納期が遅れるなどの事態を招く要因となります。
IoTの活用によって工場内のさまざまなデータを収集・蓄積できれば、需要予測や購買計画、人材管理、工程統制、品質管理、在庫管理といった生産管理の効率化と自動化が可能になります。工場全域の膨大な生産データや稼働データが統合的に管理できるため、局所的な業務効率化ではなく、製造ライン全体の総合的な生産性向上に結びつきます。
作業効率の向上
製造現場におけるIoTには、機械ではなく、従業員の身体や衣服などに装着するウェアラブルデバイスも存在します。現在活用されているソリューションとしては、音声操作が可能なヘルメット装着型のスマートグラスや、熱中症のリスクを判定する時計型デバイス、作業動作の改善点を教えてくれるスーツ型ウェアラブルデバイスなどが挙げられます。
たとえば現場のスタッフが音声で操作できるヘルメット装着型スマートグラスを活用することで、遠隔地にいる熟練工の指示を受けながら作業をすることが可能になります。その指示内容をデータとして保存し、メンバーで共有すれば、組織全体における技術力の底上げも期待できるでしょう。
品質管理の向上
センシング技術が搭載されたIoTを活用し、原材料の加工から製品の製造に至る各工程を監視することで、製品の検品や品質の検証といったプロセスをオートメーション化できます。さらにIoTは人間の目視では検知できない微細な不良や欠陥を検出できるため、より高速かつ高精度な品質管理が可能となり、品質向上による顧客満足度の最大化に寄与します。
データを利用した新規サービスの提案
IoTで収集した工場の生産データや稼働データをビッグデータとして分析し、新たな付加価値の創出につなげることも可能です。
たとえば、IoTの戦略的活用から得た知見をもとに、データ活用支援サービスを立ち上げたり、あるいはスマートファクトリー化を支援するサービスを創出するなど、データ活用から派生した新たなサービスの設計・開発が可能です。データを起点とした新たなビジネスが創出できれば、変化の加速する現代市場において、市場の競争優位性を確立する一助となります。
製造業におけるIoT導入の流れ
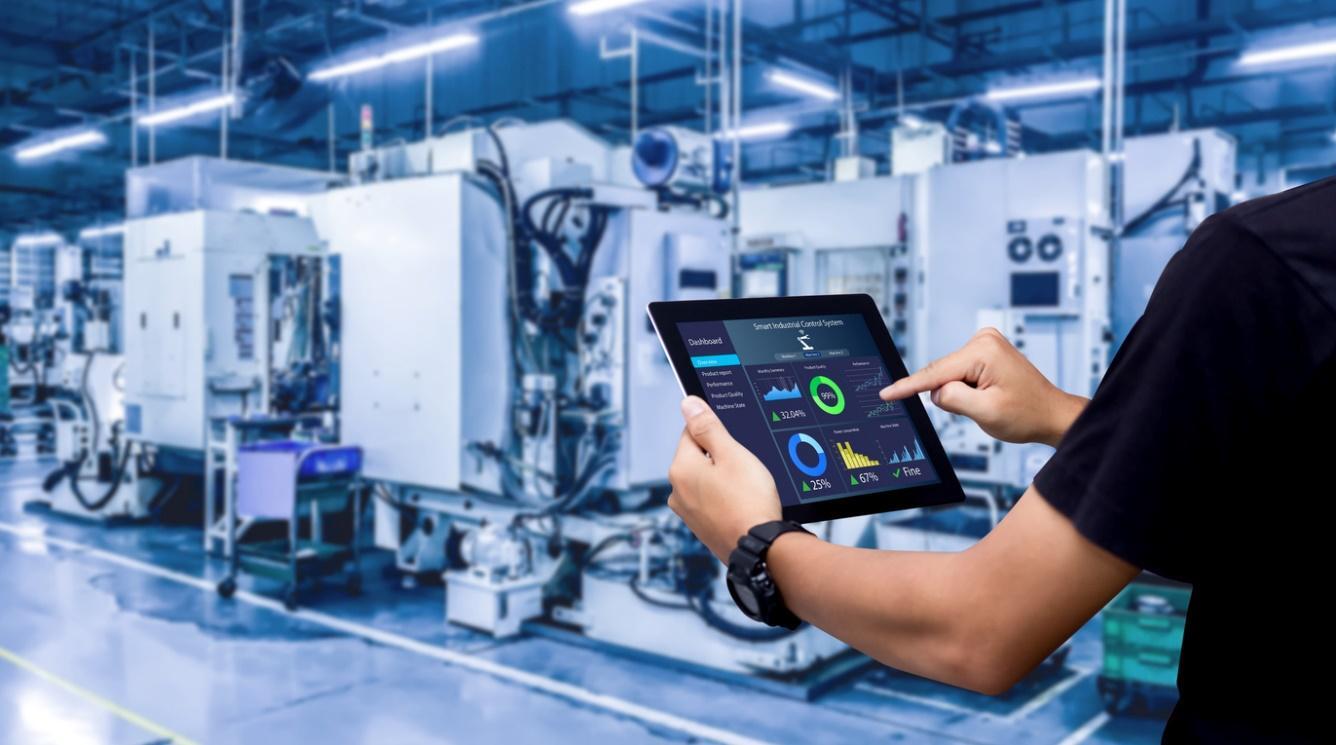
製造分野にIoTを導入する具体的な流れは、一般的には以下に挙げる3つのステップに沿って展開されます。
データの見える化に向けた分析
製造分野にIoTを導入するメリットのひとつは、工場全域におけるデータの可視化にあります。作業工程の効率化や品質管理の高精度化が可能となるのは、センシング技術が搭載されたIoTが、製造ラインの生産工程や工作機械の稼働状況などをモニタリングし、さまざまデータを収集・蓄積することで見える化するためです。したがって、製造現場にIoTを導入する際は、どのようにして自社の生産工程や稼働状況を見える化するが重要課題となります。
まずは既存の生産工程や業務プロセスを具体的な言語と数値に落とし込み、どの業務領域を可視化する必要があるのかを分析するプロセスが必要です。
機械・システムを制御する
IoTの代表的な機能が、モノの自動制御です。IoTを導入することで、遠隔地に設置した太陽光発電機の稼動コントロールや、ピッキングロボットや監視カメラの自律的な遠隔操作などが実現できます。工場内に設置された多様な機器を自動的に制御できれば、人的資源の業務負荷も大幅に軽減できます。
そのためには、機械・システムを制御する仕組みをどのように構築するかが重要な課題となります。
機械・システムを自動化する
製造分野のDXを実現するためには、さまざまなモノとインターネットを相互接続するIoTと、膨大なデータ群から規則性や法則性を導き出すAI技術の連携が不可欠です。IoTとAIを組み合わせることで、データを可視化して機器や設備を制御し、生産工程や管理業務を自動化する仕組みが構築できます。
たとえば、不良品検知の業務プロセスにIoTとAIを活用することで、製品や部品をモニタリングしてデータを収集し、異常値や外観不良などを自動で検知・検出する、といったことも可能となります。
製造業におけるIoT導入のよくある課題
このようにものづくり分野に大きな変革をもたらすIoTですが、導入するためにはいくつかの課題が存在します。ここからはIoT導入時の課題を3点に分けて紹介します。
コスト
IoTを工場全域に導入するためには、センサーやアクチュエータ(センサーが検出したデータに応じて動作を行なう装置)などの導入費に加え、ネットワーク回線を整備するコスト、システムの設計・構築やICTインフラの運用・保守管理コストなどの費用が生じます。
さらに、IoTを事業領域で戦略的に活用するためには、データの収集・分析も行なう必要があり、もし自社にICT人材がいない場合は、それらの作業を協力会社へ依頼する費用も必要になります。
こうしたコストは企業の事業規模によって大きく異なりますが、大企業のように豊富な資金調達手段をもたない中小企業にとって、IoTの導入によるスマートファクトリー化は少々ハードルが高いかもしれません。
人材不足
厚生労働省の調査(※)によると、国内の総人口は2008年の1億2,808万人をピークに下降し続けており、生産年齢人口も1992年の69.8%を頂点として、減少し続けています。日本は世界の中でもトップクラスで高齢化が進展している国でもあり、さまざまな分野で人材不足が深刻化しています。
IoTやAIを製造分野に活用するためには、テクノロジーに精通したICT人材が必要となりますが、多くの分野で人材不足が叫ばれる現在、優れたICT人材を確保するのは容易ではありません。製造分野のDXを実現するためには、ICT分野に精通した人材をどのように採用・育成するかが重要な経営課題となります。
(※)参照元:平成27年版 厚生労働白書(p.4・p.25)|厚生労働省
(https://www.mhlw.go.jp/wp/hakusyo/kousei/15/dl/all.pdf)
セキュリティリスク
IoTによって収集したデータは、組織の基幹システムやファイルサーバー、クラウドストレージなどに蓄積されます。こうしたデータを保管しているコンピュータがサイバー攻撃の対象となった場合、機密データの漏えいが危惧されます。2016年には、IoT機器を狙ったマルウェア「Mirai」が猛威をふるった事例もあります。IoTを活用するためには年々高度化かつ多様化するサイバー攻撃に耐えきれるシステム環境の構築が必要です。
まとめ
競争が激化する現代の製造分野においてはDXが不可欠であり、そのためにはIoTの戦略的活用が欠かせません。IoTを導入することによって、品質管理の省人化や設備保全の自動化などが可能となり、人件費の削減や製造ライン全体の生産性向上が可能になります。新しい時代に即したイノベーティブな生産体制を構築するためにも、まだ未導入の企業は、IoTに取り組むべきといえるでしょう。
製造業のスマートファクトリー化をデジタル技術から支援
日本の製造業は人材不足や老朽化した生産設備の維持、技能継承など、さまざまな問題を抱えており、これらに対応するため、生産性の向上が喫緊の課題となっています。NTT東日本は、「デジタル技術」と「セキュアなインフラ環境」によって、工場のデジタル化(スマートファクトリー化)をご支援。製造業の生産性向上をサポートします。
連載記事一覧
- 第1回 製造業におけるDX(デジタルトランスフォーメーション)の必要性とは?事例も合わせて紹介 2022.03.04 (Fri)
- 第2回 製造業における機械学習の事例および活用可能な機械学習技術について解説 2022.03.04 (Fri)
- 第3回 工場のスマートファクトリー化を進める課題とは何か 2022.03.04 (Fri)
- 第4回 ローカル5Gとは? 工場で導入する方法や事例を解説 2022.03.04 (Fri)
- 第5回 ファクトリーオートメーション(工場の自動化)とは?今後はどうなる? 2022.03.04 (Fri)
- 第6回 スマートファクトリーの土台となる工場のネットワークとは? 2022.03.04 (Fri)
- 第7回 ファクトリーオートメーションの事例や企業、今後とは? 2022.03.04 (Fri)
- 第8回 2021年6月より義務化! 食品事業者が知っておくべきHACCPの基本と事例を紹介 2022.03.04 (Fri)
- 第9回 製造業で注目を集めている「Anywhere Operations」とは?概要などについて解説 2022.03.04 (Fri)
- 第10回 製造業における情報セキュリティリスクの高まりとその対策方法 2022.03.04 (Fri)
- 第11回 製品開発のDX化のカギを握るCAE解析とは? 2022.03.04 (Fri)
- 第12回 製造業で導入が始まっているデジタルツインとは 2022.03.04 (Fri)
- 第13回 インダストリー4.0とは?概要や課題、事例などを紹介 2022.03.04 (Fri)
- 第14回 製造プロセスの最適化が期待できるPLMソリューションとは 2022.03.04 (Fri)
- 第16回 製造業を取り巻く現状と考えられる課題とは? その対策についても解説2023.01.30 (Mon)
- 第18回 工場を見える化するには? メリットや具体的な方法を紹介2023.01.30 (Mon)
- 第19回 製造業におけるヒューマンエラー対策とは? エラーが起こる原因も解説2023.01.30 (Mon)
- 第25回 製造業の今後は? 現状の課題や生き残るための手段を解説2023.01.30 (Mon)
- 第42回 事例から学ぶ、被害最大の「製造業」ランサムウェア対応2024.03.29 (Fri)
- 第43回 【用語解説】製造業が必ず押さえたい3つのセキュリティトレンド2024.03.29 (Fri)
- 第44回 工場停止で数千万の損害も、製造業に"すぐ必要"なサイバー攻撃対策とリスクアセスメント診断2024.03.29 (Fri)
- 第45回 自社だけ万全でも意味がない、サプライチェーン攻撃を防ぐには2024.03.29 (Fri)
- 第46回 ITとの違いから学ぶ、OTセキュリティ強化で知るべきポイント2024.03.29 (Fri)
- 第20回 製造業における品質管理の重要性とは? 品質対策のポイントも解説2023.01.30 (Mon)
- 第47回 突然、取引停止?工場セキュリティ未対策のリスク2024.03.29 (Fri)
- 第48回 OTセキュリティ強化の必読書、経産省発行のガイドラインを読み解く2024.03.29 (Fri)
- 第49回 製造業にも遵守義務、EUサイバーレジリエンス法とは?2024.03.29 (Fri)
- 第50回 ゼロからはじめる工場のセキュリティ対策2024.03.29 (Fri)
- 第21回 トレーサビリティとは? 種類や製造業におけるメリットを解説2023.01.30 (Mon)
- 第23回 工場に求められる安全対策とは?その重要性と対策のポイントを紹介2023.01.30 (Mon)
- 第50回 OTとITの融合を進めるために考えるべきこととは?2024.08.09 (Fri)
- 第51回 ニーズを捉えるための「多品種少量生産」とは?2024.08.09 (Fri)
- 第27回 工場を見える化することで得られるメリットは? 具体的な導入の流れも解説2023.01.30 (Mon)
- 第28回 工場の省人化とは? 実現するための具体的な方法を解説2023.01.30 (Mon)
- 第31回 生産管理とは? 目的や内容からシステムの選び方までわかりやすく解説2023.01.30 (Mon)
- 第32回 製造業の生産性を向上させるメリットやその際の着目ポイントなどを解説2023.01.30 (Mon)
- 第30回 製造業で品質向上をめざすには? 解決すべき課題について解説2023.01.30 (Mon)
- 第33回 生産管理が属人化する理由とは? 解消方法と標準化するメリットを解説2023.01.30 (Mon)
- 第35回 製造業におけるコスト削減のポイントとは? 具体例や今後の動向を解説2023.01.30 (Mon)
- 第37回 製造業における働き方改革とは? メリットや成功のポイントを解説2023.01.30 (Mon)
- 第36回 SCMとは? メリット・デメリットやERPとの違いについて解説2023.01.30 (Mon)
- 第38回 【製造業向け】RPA導入のメリットや注意点とは?2023.01.30 (Mon)
- 第29回 工場にAIを導入するメリット・デメリット、失敗するケースを解説2023.01.30 (Mon)
- 第34回 QCDとは? 生産管理の考え方やQCDの改善法について解説2023.01.30 (Mon)
- 第15回 工場の改善アイデア・事例5選! 業務改善を成功させるコツや実施手順も紹介2023.01.30 (Mon)
- 第17回 製造業のヒヤリハット事例5選 報告書の書き方や対策の進め方2023.01.30 (Mon)
- 第22回 製造業にIoTを導入するメリットとは? 事例や課題を解説2023.01.30 (Mon)
- 第24回 生産管理はAIでどう変わる? 製造業におけるAIの活用事例を紹介2023.01.30 (Mon)
- 第26回 工場は深刻な人手不足。その原因と5つの対策法とは2023.01.30 (Mon)
- 第39回 増えている製造業へのサイバー攻撃! 理由や対策法を徹底解説2023.02.15 (Wed)
- 第40回 工場の現場をペーパーレス化するメリットとは? 導入ステップやツールを紹介2023.02.15 (Wed)
- 第41回 多能工化とは何か? メリット・デメリットと失敗しない進め方を解説2023.02.15 (Wed)