2023.01.30 (Mon)
ICTで製造業はどのように変わるのか(第30回)
製造業で品質向上をめざすには? 解決すべき課題について解説
製造業の現場では、品質向上をめざす取り組みが数多く行われています。この記事では「見える化」など、具体的な取り組み内容やメリットについて詳しく解説します。一方で、品質管理は少子高齢化や業務の属人化など、立ちはだかる課題も多いため、きちんと確認しておくことが重要です。製造業で品質向上に取り組んでいくには、どのようなポイントに注目すべきなのかも紹介します。
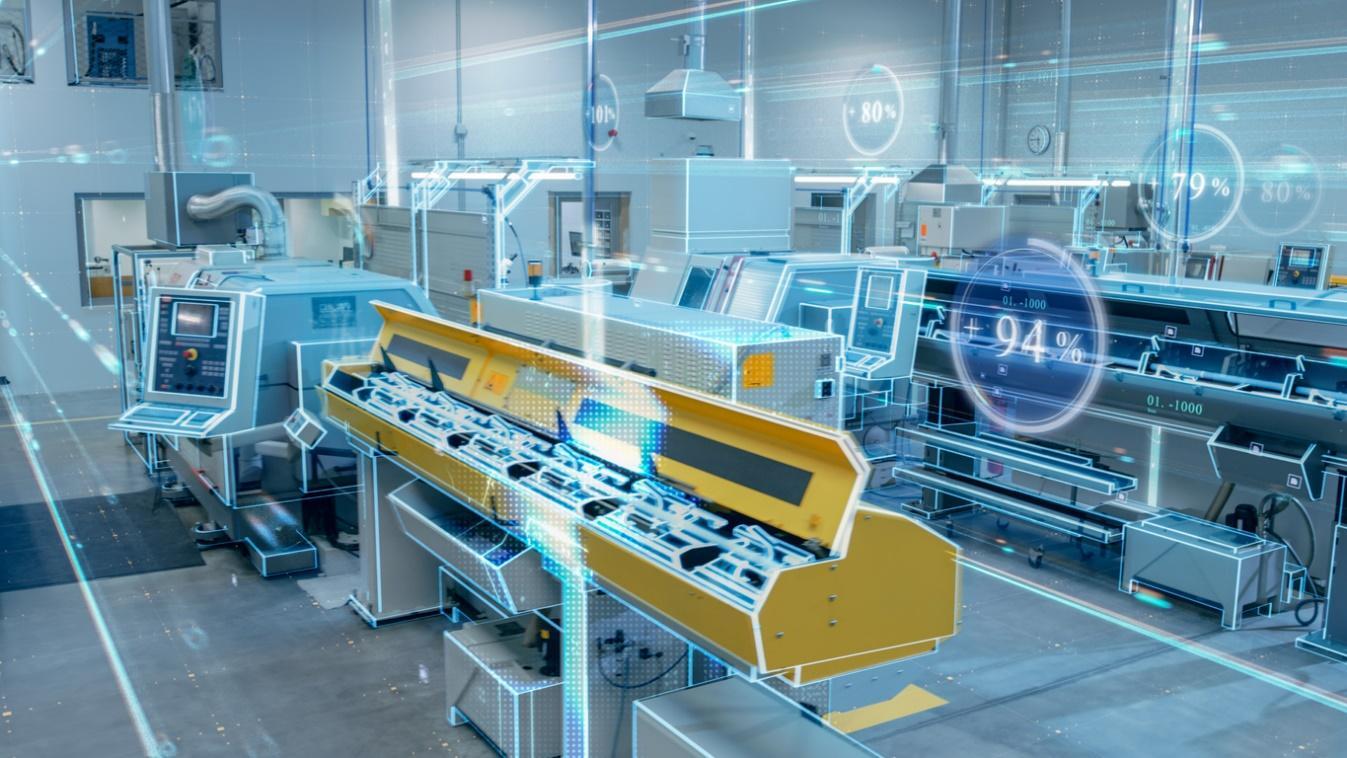
製造業で取り入れられている品質向上の取り組みとは
製造業やものづくりの現場では、品質管理が不可欠です。生産環境の維持だけでなく、製品の品質を上げてクオリティの高い製品をユーザーに届けるべく、さまざまな取り組みが行われています。ここでは、どのような取り組みがあるのかを具体的に紹介します。
工場の見える化を実施する
工場でトラブルが起きた際、原因が究明できず解決できなかったり、解決策にたどり着くまで時間がかかるような状況は、できるだけ避けたいところです。トラブルが起こる可能性を抱えたまま製品を製造することは、生産性が上がらず、コストがかさむ要因になってしまいます。
こうした課題を解決するには、まず工場の稼働状況を「見える化」するのが有効です。工場の見える化とは、稼働状態や生産の進捗、実績などの情報をわかりやすく示すことでスピーディな意思決定を促進したり、継続的な品質改善へつなげる施策です。多くの従業員が働く現場では、それぞれが同じ生産目標に向かって、やるべきことを把握していることが重要です。近年はデジタル技術を活用して見える化を実現した工場の事例として、「スマートファクトリー」にも注目が集まっています。
では、生産工程を見える化すると、どのようなメリットが生まれるのでしょうか。たとえば、製品に不具合が発生する前の段階で異常に気付いたり、コスト削減につながるムダやムラを発見できます。これらのメリットは結果的に業務負担軽減につながるため、離職率の低下も防げるでしょう。
見える化は、主にインターネットを介してさまざまな機器を通信可能にするIoT(Internet of Things:モノのインターネット)を導入することで実現できます。工場内にある設備や機器からあらゆるデータを収集して分析すれば、これまで疑問に感じなかった業務プロセスにも改善すべき点が見えてくる可能性があります。ユーザーのニーズにあわせた新製品開発もスムーズに行えるようになり、結果的に顧客満足度の向上、ファンやリピーターの増加へとつながります。つまり、IoTの活用は生産性のみならず品質も高められるメリットがあるのです。
製造のプロセスに5Sを取り入れる
製造業やサービス業でよく使われる「5S」は、品質管理のために使われる手法のひとつで、「整理・整頓・清掃・清潔・しつけ」の5要素のことを示します。いずれも頭文字がSで始まっていることから、5Sと呼ばれています。
「整理」は、必要なモノを見極め、不要なモノを捨てることでムダをなくします。「整頓」は、どこに何を配置するのかを定め、その状態を維持することで最終的に業務効率化につなげることです。「清掃」は、きれいに掃除や点検をすることで、不具合を見付けやすくします。「清潔」は業務環境を良好な状態に維持すること、「しつけ」は守るべきルールの遵守を徹底することです。これらが総合的に効果を発揮すれば、生産性向上に期待できます。
5Sを製造プロセスに取り込むことは、単にきれいに掃除したり、整然と並べることだけを意味しているわけではありません。「真に必要なモノに絞り込み、仕事をしやすくし、職場環境を整えていく」といった目的を意識し、実践することが大切です。業務プロセスの中に隠れていたムダやムラをなくせば生産性向上につながるとともに、ヒューマンエラーも減らせるようになるでしょう。
4Mの観点で品質管理を行う
5Sと同じような意味で、製造業では品質管理や生産管理において「4M」と呼ばれる用語もよく使われます。物事をMan(人)、Machine(機械)、Material(材料)、Method(方法)と4つの要素に分けて製品の品質を維持、向上させようとする手法です。
通常、製造のプロセスにおける不良品は、複数の背景や原因が重なり合って発生することを想定しなければなりません。不良品の生産に至った真の原因を突き止める際に使われるのが、4Mです。4Mを基にすればもれなくダブりなく(MECE)、原因をチェックできるため、不良品の生産工程も正確に分析できます。品質管理の業務では、4Mの姿勢や考え方を意識するとよりスムーズに品質改善へとつなげられるでしょう。
品質管理を行ううえで立ちはだかる課題とは
製造業での品質管理には、さまざまなハードルが存在します。現場でよくありがちな課題について、ここでは5つの注意すべきポイントを解説します。
人手不足に伴う属人化
少子化が進む中で、他業界と同じく製造業も従業員の高齢化とともに深刻な人手不足に悩まされています。総務省が公表している「情報通信白書令和2年度版」によると、2018年における日本の就業者数約6,664万人のうち、製造業の就業者数は約1,060万人で、2008年と比べると約91万人減、全就業者に対する割合は18%から15.9%に減少していることがわかります。
現場の人手が不足していると、特定の業務は属人化する傾向にあり、異動や退職による引き継ぎ時にノウハウやナレッジが蓄積されにくくなります。品質向上のために人員を配置することも困難なため、ICTの活用など、限られたリソースをいかに効率的に使うかに焦点を置き、早急に対策を検討する必要があるでしょう。
急な仕様変更による負担増大
製造プロセスの管理で、Excelなどのローカルファイルで各種データを管理する企業は少なくないでしょう。その場合、急な仕様変更などが発生するたびにデータが増えていきます。結果、データの確認に多くの手間や時間がかかり、従業員の稼働も増える可能性があります。
Excelは普及率が高く、多くの人が気軽に使えるメリットはあるものの、膨大なデータを収集し、分析・管理する目的には向きません。製造業における生産管理業務では、増え続けるデータを一元的に管理できるシステムやソフトウエアを導入するとよいでしょう。
脆弱な管理体制
製造業で品質向上をめざすためには、現場の全体像や現状課題を的確に把握することが大前提です。しかし、特に中小企業では従業員の適正な配置やコストなど、さまざまな管理体制が整っていないことにより、品質向上にまで手が回っていないケースが散見されます。これでは、現場の状況把握に大きな手間がかかるほか、品質向上に向けた取り組みがあいまいになってしまうでしょう。
製造プロセスにおける生産体制を強化する前には、社内の管理体制が整っているかどうかをまず確認し、脆弱な点があれば早急に改善することが必要です。
品質向上のための施策が定着しない
品質改善に向けた施策を展開しても、経営陣や一部の部署のみが盛り上がり、現場の従業員から協力を得られないことはよくあります。施策が定着しなければ、これまで費やした時間や労力が報われません。
品質向上施策を実施する前に、「なぜ品質を改善する必要があるのか」といった目的やビジョンを全従業員に伝え、認識をあわせることが重要です。現場との密なコミュニケーションが、成功への近道となります。
品質改善策の効果を検証していない
品質改善の施策を実施しても、不良品がどのくらい減ったのか、コストはどれだけ削減できたのかといった効果を検証しなければ意味がありません。改善施策はあくまで手段であり、品質向上といった本来の目的の達成度を確認することで、施策に意義が生まれます。
しかし、日々の業務に追われ、施策を検証できない工場は少なくありません。あるいは、時間は十分にあったとしても、手間やコストがかかるため検証できていないケースもあるでしょう。効果検証を着実に実施し、新たな課題が見つかれば次のアクションにつなげることが重要です。
通常、製品の品質は複数の要素によって決まります。品質を改善するには、どの要素を強化すればよいのかを見極めなければなりません。できるだけスムーズに改善していくためには、生産工程を見える化することが重要になるでしょう。具体的には、マインドマップや作業工程表を使って共有する方法が考えられます。
製造業で品質向上を実現させるためのポイント
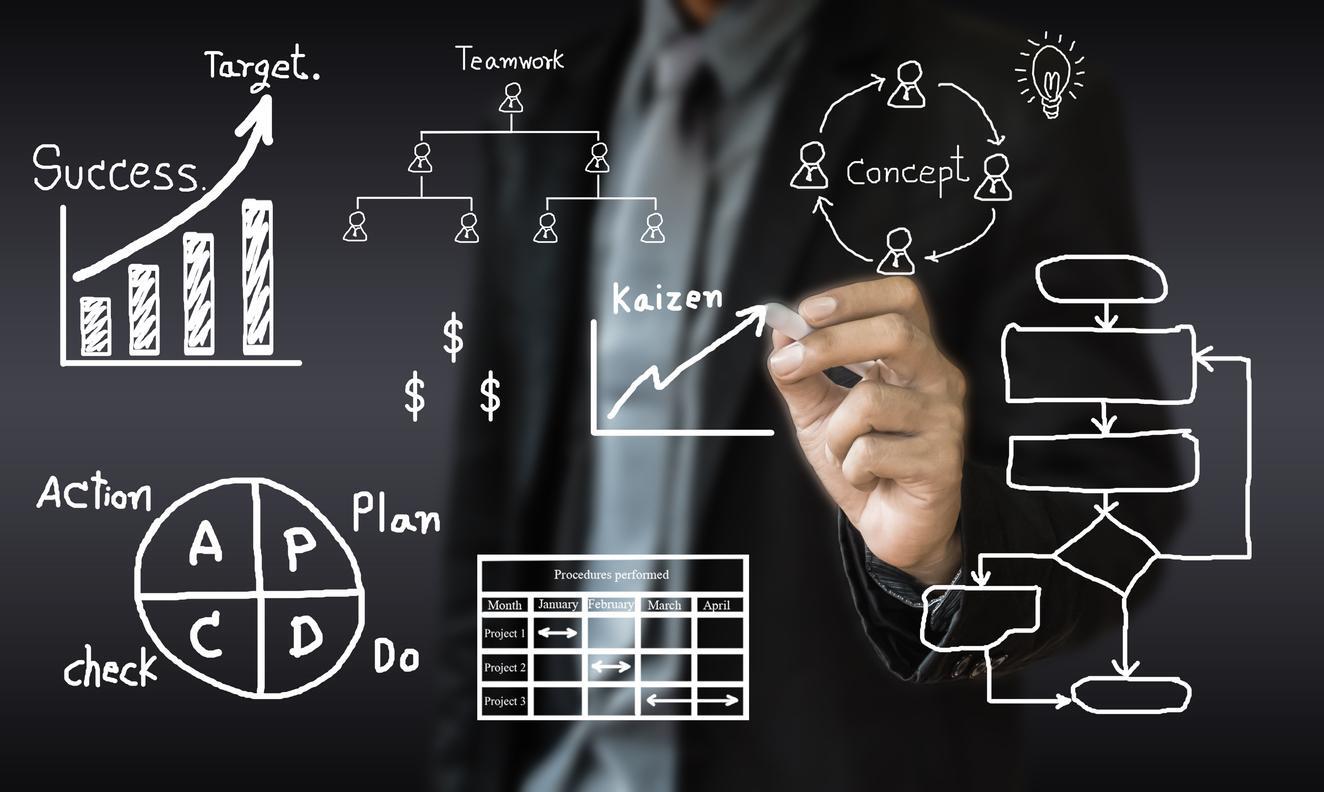
ここでは、製造業で製品の品質を向上させるために、意識して取り組むべきふたつのポイントを紹介します。
手順書を整備して業務を標準化する
前述のように、製造業には人手不足に陥っている企業が多く、業務がベテラン従業員によって属人化している例が見られます。しかし、そのままでは業務プロセスの改善は見込めません。
業務効率化を図り、生産性を向上させるためには、特定の従業員だけが「知っている」、「できる」のではなく、誰でも同じように一定のクオリティで業務を理解し、遂行できるように標準化する必要があります。
そのカギを握るのが、作業手順書です。これまで暗黙の了解で行われてきた業務を言語化し、作業の流れを図式などで表すことで、標準化が実現できます。適切な作業手順書があれば、誰もが業務を理解できるようになるほか、限られた人的リソースであってもスムーズに業務を進められる可能性が高まります。
AIの導入を検討する
もうひとつのポイントは、AIの導入です。そもそもAIとは、1956年、計算機科学者・認知科学者のジョン・マッカーシー教授が提唱したことから世界へ広まりました。「Artificial Intelligence(アーティフィシャル・インテリジェンス)」の略称で、日本語では「人工知能」と訳されます。ディープラーニングに代表される技術革新もあり、コンピューターが人間のように自ら学習することによって、問題解決を効率化できる技術として注目されています。
製造業の現場にAIを導入すると、品質管理の観点で、さまざまなメリットが生まれます。たとえば、これまで生産した製品の外観検査はおもに人が目視で行っていました。しかし、AIを使って自動的に不具合を検出するシステムを使えば、品質の基準が一定となり不良品率も減るでしょう。
ヒューマンエラーを気にせずに安全性も確保できるため、従業員の負担軽減につながるのもAI導入の利点です。業務の効率化によって一人ひとりのパフォーマンスや仕事へのモチベーションが上がれば、エンゲージメントを強化でき離職率低下を防げるようにもなります。少ない人員であっても、生産性を上げられるようになるのは大きなメリットです。
労働力の減少が進み、今後も製造業を取り巻く環境はますます厳しくなると考えられます。IoTやAIなどの技術を積極的に導入し、全社一丸となって品質向上に取り組むことで、業務効率化や生産性向上へつなげていきましょう。
まとめ
少子高齢化が進む中、製造業ではIoTを活用した「見える化」などさまざまな品質向上の取り組みが実践されています。その際、製造プロセスに「5S」の考え方を取り入れたり、「4M」の観点をもって管理することで、よりスムーズに品質改善へつなげられるでしょう。品質管理にはさまざまなハードルがあるものの、手順書による業務標準化やAI活用、システム導入による一元管理がキーとなります。これらは、製造業のDX化、ひいてはスマートファクトリー化につながるものです。
以下の資料では、製造業で近年注目されているスマートファクトリー化についてわかりやすく解説しています。ぜひ併せてご覧ください。
製造業のスマートファクトリー化をデジタル技術から支援
日本の製造業は人材不足や老朽化した生産設備の維持、技能継承など、さまざまな問題を抱えており、これらに対応するため、生産性の向上が喫緊の課題となっています。NTT東日本は、「デジタル技術」と「セキュアなインフラ環境」によって、工場のデジタル化(スマートファクトリー化)をご支援。製造業の生産性向上をサポートします。
連載記事一覧
- 第1回 製造業におけるDX(デジタルトランスフォーメーション)の必要性とは?事例も合わせて紹介 2022.03.04 (Fri)
- 第2回 製造業における機械学習の事例および活用可能な機械学習技術について解説 2022.03.04 (Fri)
- 第3回 工場のスマートファクトリー化を進める課題とは何か 2022.03.04 (Fri)
- 第4回 ローカル5Gとは? 工場で導入する方法や事例を解説 2022.03.04 (Fri)
- 第5回 ファクトリーオートメーション(工場の自動化)とは?今後はどうなる? 2022.03.04 (Fri)
- 第6回 スマートファクトリーの土台となる工場のネットワークとは? 2022.03.04 (Fri)
- 第7回 ファクトリーオートメーションの事例や企業、今後とは? 2022.03.04 (Fri)
- 第8回 2021年6月より義務化! 食品事業者が知っておくべきHACCPの基本と事例を紹介 2022.03.04 (Fri)
- 第9回 製造業で注目を集めている「Anywhere Operations」とは?概要などについて解説 2022.03.04 (Fri)
- 第10回 製造業における情報セキュリティリスクの高まりとその対策方法 2022.03.04 (Fri)
- 第11回 製品開発のDX化のカギを握るCAE解析とは? 2022.03.04 (Fri)
- 第12回 製造業で導入が始まっているデジタルツインとは 2022.03.04 (Fri)
- 第13回 インダストリー4.0とは?概要や課題、事例などを紹介 2022.03.04 (Fri)
- 第14回 製造プロセスの最適化が期待できるPLMソリューションとは 2022.03.04 (Fri)
- 第16回 製造業を取り巻く現状と考えられる課題とは? その対策についても解説2023.01.30 (Mon)
- 第18回 工場を見える化するには? メリットや具体的な方法を紹介2023.01.30 (Mon)
- 第19回 製造業におけるヒューマンエラー対策とは? エラーが起こる原因も解説2023.01.30 (Mon)
- 第25回 製造業の今後は? 現状の課題や生き残るための手段を解説2023.01.30 (Mon)
- 第42回 事例から学ぶ、被害最大の「製造業」ランサムウェア対応2024.03.29 (Fri)
- 第43回 【用語解説】製造業が必ず押さえたい3つのセキュリティトレンド2024.03.29 (Fri)
- 第44回 工場停止で数千万の損害も、製造業に"すぐ必要"なサイバー攻撃対策とリスクアセスメント診断2024.03.29 (Fri)
- 第45回 自社だけ万全でも意味がない、サプライチェーン攻撃を防ぐには2024.03.29 (Fri)
- 第46回 ITとの違いから学ぶ、OTセキュリティ強化で知るべきポイント2024.03.29 (Fri)
- 第20回 製造業における品質管理の重要性とは? 品質対策のポイントも解説2023.01.30 (Mon)
- 第47回 突然、取引停止?工場セキュリティ未対策のリスク2024.03.29 (Fri)
- 第48回 OTセキュリティ強化の必読書、経産省発行のガイドラインを読み解く2024.03.29 (Fri)
- 第49回 製造業にも遵守義務、EUサイバーレジリエンス法とは?2024.03.29 (Fri)
- 第50回 ゼロからはじめる工場のセキュリティ対策2024.03.29 (Fri)
- 第21回 トレーサビリティとは? 種類や製造業におけるメリットを解説2023.01.30 (Mon)
- 第23回 工場に求められる安全対策とは?その重要性と対策のポイントを紹介2023.01.30 (Mon)
- 第50回 OTとITの融合を進めるために考えるべきこととは?2024.08.09 (Fri)
- 第51回 ニーズを捉えるための「多品種少量生産」とは?2024.08.09 (Fri)
- 第27回 工場を見える化することで得られるメリットは? 具体的な導入の流れも解説2023.01.30 (Mon)
- 第28回 工場の省人化とは? 実現するための具体的な方法を解説2023.01.30 (Mon)
- 第31回 生産管理とは? 目的や内容からシステムの選び方までわかりやすく解説2023.01.30 (Mon)
- 第32回 製造業の生産性を向上させるメリットやその際の着目ポイントなどを解説2023.01.30 (Mon)
- 第30回 製造業で品質向上をめざすには? 解決すべき課題について解説2023.01.30 (Mon)
- 第33回 生産管理が属人化する理由とは? 解消方法と標準化するメリットを解説2023.01.30 (Mon)
- 第35回 製造業におけるコスト削減のポイントとは? 具体例や今後の動向を解説2023.01.30 (Mon)
- 第37回 製造業における働き方改革とは? メリットや成功のポイントを解説2023.01.30 (Mon)
- 第36回 SCMとは? メリット・デメリットやERPとの違いについて解説2023.01.30 (Mon)
- 第38回 【製造業向け】RPA導入のメリットや注意点とは?2023.01.30 (Mon)
- 第29回 工場にAIを導入するメリット・デメリット、失敗するケースを解説2023.01.30 (Mon)
- 第34回 QCDとは? 生産管理の考え方やQCDの改善法について解説2023.01.30 (Mon)
- 第15回 工場の改善アイデア・事例5選! 業務改善を成功させるコツや実施手順も紹介2023.01.30 (Mon)
- 第17回 製造業のヒヤリハット事例5選 報告書の書き方や対策の進め方2023.01.30 (Mon)
- 第22回 製造業にIoTを導入するメリットとは? 事例や課題を解説2023.01.30 (Mon)
- 第24回 生産管理はAIでどう変わる? 製造業におけるAIの活用事例を紹介2023.01.30 (Mon)
- 第26回 工場は深刻な人手不足。その原因と5つの対策法とは2023.01.30 (Mon)
- 第39回 増えている製造業へのサイバー攻撃! 理由や対策法を徹底解説2023.02.15 (Wed)
- 第40回 工場の現場をペーパーレス化するメリットとは? 導入ステップやツールを紹介2023.02.15 (Wed)
- 第41回 多能工化とは何か? メリット・デメリットと失敗しない進め方を解説2023.02.15 (Wed)