2023.01.30 (Mon)
ICTで製造業はどのように変わるのか(第25回)
製造業の今後は? 現状の課題や生き残るための手段を解説
日本の製造業は、新型コロナウイルスの感染拡大や少子高齢化による労働人口の減少などにより、さまざまな課題を抱えています。それらの課題を解決するためには、製造業ならではの技術を継承する方法や、今後も続く人口減少への対応が重要です。本記事では、製造業の現状と課題に触れながら、そこから見える製造業が取るべき対策を紹介します。
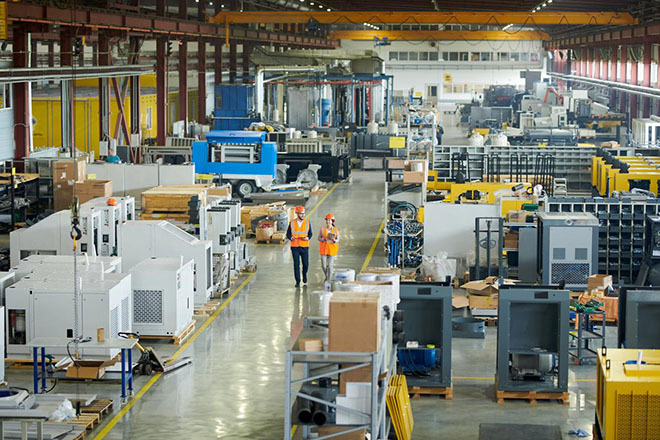
製造業が直面している現状
近年の製造業は、新型コロナウイルスの感染拡大や半導体不足などの影響を受けて大きく落ち込んでいます。経済産業省・厚生労働省・文部科学省が2022年5月に発表した「ものづくり白書」においても、さまざまな要因により売上高や営業利益が減少傾向にあるとされています。
新型コロナウイルスの感染拡大
2020年から感染が急拡大した新型コロナウイルスは、世界中の製造業に大きな影響を与えました。感染拡大によりサプライチェーンが寸断されたため、世界中の工場に部品が届かないケースが発生しています。感染拡大初期には、原材料や部品の調達ができず、生産を停止する企業も多く見られました。
こうした背景もあり、業績の落ち込みから生産を縮小したメーカーもあります。日本の製造業者の売上も、2020年に売上が大きく下降しています。2021年に入ってからは、半数ほどの企業が上昇に転じていますが、一方で低迷したままの企業も多く存在します。
ところが2022年に入ると、世界的な半導体不足の影響を受けて、生産は再び縮小傾向にあります。中でも半導体に関しては、増加する需要に対して輸出管理規制の強化や災害・事故などにより供給量が不足し、幅広い業種に悪影響が出ています。
製造業における4つの課題
日本の製造業を取り巻く環境はここ数年で大きく変化する中、さらに多くの問題が顕在化しつつあります。具体的には、「人手不足」「自動化の遅れ」「技術継承問題」「人件費の高騰」です。製造業が今後も生き残るためには、これらの課題と真摯に向き合い、対応策を講じなくてはなりません。
人手不足
少子高齢化が加速する日本では、さまざまな業界で人手不足が叫ばれていますが、製造業においては特にその傾向が顕著です。経済産業省、厚生労働省、文部科学省が共同で取りまとめた「2022年版ものづくり白書」によれば、2021年における全産業に占める製造業の就業者数の割合は、2002年と比較して3.4ポイント低下しています。
さらに、製造業では34歳以下の若年就業者が20年間で約121万人減少しています。対して、65歳以上の高齢就業者数は20年間で約33万人増加しており、2022年時点の就労者数は若年就業者が25%、高齢就業者が9%の割合で落ち着いています。
このまま人手不足の状況が続けば労働環境が悪化し、従業員のモチベーション低下、離職率増加により、さらなる人手不足に陥るという悪循環が懸念されます。そうなれば生産性の低下は免れず、事業の縮小、ひいては国力の衰退にもつながるでしょう。
日本は今後も少子高齢化による労働人口の減少が続くと見られており、人手不足の抜本的な解決を図るには、雇用だけでなく多角的な観点からアプローチが求められます。
自動化の遅れ
手作業の多い製造業では、「DX(デジタルトランスフォーメーション)」による業務自動化が、課題解決に貢献することが期待されています。
DXとは、AIやIoTなど先端技術の活用により企業変革を図り、競争優位性の確立をめざすことで、日本でもDX推進の取り組みが進んでいます。製造業にAIを導入することで、これまで手作業で行っていた業務を機械に任せ、手が空いた従業員がコア業務や有人対応を要する業務に回ることが可能になります。加えて、作業品質の均一化や正確性の向上、現場従業員の負担軽減も期待できます。
ところが、日本の製造業におけるDXは、ICT活用に対する経営層の理解不足や、システムのレガシー化、ICT人材の確保の難しさなどの問題から、諸外国と比べて普及が遅れているのが実情です。加えて、IoT機器やAIシステムを導入するためには多額のコストを要するため、金銭的余裕がない中小企業では導入しづらいのが実情です。
もっとも、近年では製造業DXに対する意識が向上してきているのも事実です。一般社団法人 日本情報システムユーザー協会(JUAS)が実施した「企業IT動向調査2021(2020年度調査)」によると、IT投資で解決したい重点課題として6割強の企業が「業務プロセスの効率化とスピードアップ」を、4割強の企業が「ビジネスプロセスの変革」を挙げています。
さらに、2021年における製造業のIT投資額は、前年比で約0.1兆円のマイナスながらも、一部の業種では増加しているところも多く、今後の伸びが期待されます。
加えて、中小企業庁がとりまとめた「2021年版 中小企業白書」では、製造分野の中小企業におけるデジタル化への意識が、新型コロナウイルス流行前後で大きく変化していることも示されています。流行後の調査では、約65%の企業がデジタル化の優先順位を「高い」もしくは「やや高い」に位置付けており、DXに対する前向きな姿勢がうかがえます。
技術承継問題
企業独自の知見やノウハウを共有・継承していくことは、事業継続の観点から多くの企業で重視されています。もちろん製造業も例外ではありませんが、技術承継に問題を抱えているケースが少なくありません。
まずは少子高齢化により、次代を担う若手人材が不足している問題が挙げられます。技術承継をしようにも、そもそも後継者がいなければ話になりません。しかし、ただでさえ人手不足な製造業では、生産性との兼ね合いで人材育成に時間や人員を割けず、せっかく採用した若手人材が育たないうちに退職してしまう恐れがあります。
さらに、終身雇用制度から成果主義制度への変化が原因となり、技術を有した従業員がいなくなる場合もあります。成果主義を採用している場合、高い技術を持つ従業員が定年まで働かずに転職するケースがあるため、技術承継ができていないと、技術そのものも失われる可能性があります。
技術承継が適切に行われなければ、生産効率の低下や、新製品の開発が難しくなるなどの問題が生じます。今後の企業経営に悪影響を及ぼす恐れも十分に考えられます。
人件費の高騰
前述の人材不足に関連して、人件費の高騰も製造業にとって大きな課題です。日本の労働人口が減少している現在、安価な給与では、企業が人材を獲得することも、雇用を継続することも困難です。
このような状況の中、競合他社に先んじて優秀な人材をより多く獲得するためには、給与や福利厚生などの面で好待遇をアピールすることが重要です。
製造業が取るべき対策
こうした課題を踏まえ、製造業が取るべき対策としては、「ICT化」や「ナレッジマネジメントの構築」、「無駄の削減」が考えられます。この3つの対策で業務効率化を図ることで、従業員の作業負担を減らしつつ、生産性の向上が可能です。
ICT化
ICT化は、企業規模を問わずこれからの製造業に必要な変化です。たとえばIoT機器を導入することで、製品を生産する機械の稼働状況や製造工程、故障箇所の有無など、工場内のあらゆるデータを自動的に収集して保存できます。必要なデータを抽出して確認・分析もできるため、製造ラインの稼働状況や生産効率まで幅広く把握することが可能です。
ロボットもICT機器として、多くの企業が導入を進めています。ロボットの導入により、製造や検査などの作業工程を自動化できるため、生産性の向上が期待できます。加えて、品質のばらつきやヒューマンエラーが生じにくいメリットもあります。
ナレッジマネジメントの構築
企業の技術承継をスムーズに行うためには、技術に関する知識やノウハウをチームで共有することが大切です。そのためには、ベテランの従業員が蓄積している知識や経験、ノウハウなどの暗黙知を言語化して、手順書やマニュアル、動画や写真などに残す「ナレッジマネジメント」を構築する必要があります。
ナレッジマネジメントを構築することで、誰もが理解・習得できるデータやマニュアルを社内で共有したり、従業員が検索システムで必要な情報を簡単に閲覧できるようになります。手順を何度も確認できるため、技術承継も無理なく行えるでしょう。
無駄の削減
製造業の現場においては、「加工」「在庫」「不良・手直し」「手待ち」「造りすぎ」「動作」「運搬」の7つの無駄が生じやすいとされています。これらはそれぞれの頭文字を取って「かざふてつどう」と呼ばれ、製造業が業務効率化をめざすうえで意識すべき標語となっています。
この「かざふてつどう」の標語を意識することで、不要な加工プロセスや加工方法がないか、余剰在庫が保管スペースを圧迫していないか、不良品の発生防止のために品質管理が適切に行われているかなどがチェックでき、無駄の削減につながります。
第5次産業革命とスマートファクトリーの関係
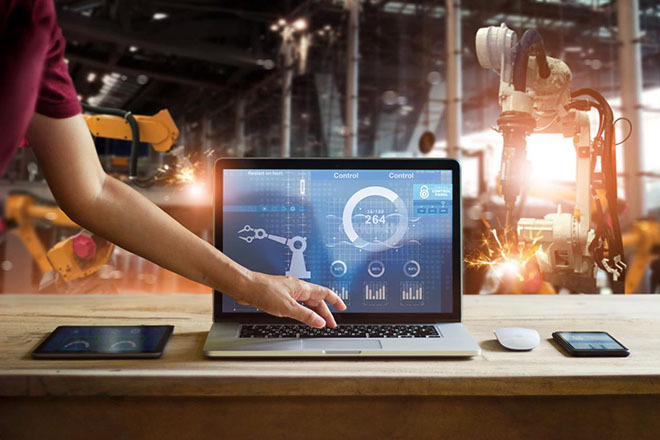
製造工程にIoT機器やAIなどのICTを取り入れ、生産の自動化をめざす技術革命のことを、「第4次産業革命(インダストリー4.0)」と呼びます。現在、多くの企業で検討・導入されているスマートファクトリー(後述)も、この第4次産業革命に含まれます。
この第4次産業革命を、さらに推し進めた技術革新が「第5次産業革命」です。第5次産業革命は、人と機械の協働をめざすもので、製品の企画開発などの工程に加え、従業員の近くに配置する小型ロボット「コボット」を用いるなど、製造ラインに人と機械が混在して働く状況を想定したプランとなります。
スマートファクトリーとは
第4次産業革命において、AIやIoT、ロボットなどのICTを活用し、設備稼働状況の可視化や保守・保全業務の効率化、製造プロセスの改善といった変革を実現する工場のことを「スマートファクトリー」と呼びます。スマートファクトリーでは、工場機器に取り付けられたIoTセンサーが設備の情報を自動的に収集・蓄積し、そのデータをAIが分析することで、あたかも工場自体が自律的に判断・行動しているかのような、高度なオートメーションが可能になります。
スマートファクトリーは作業の再現性や一貫性が高いため、同一の製品を効率的に大量生産するケースに適しています。
工場をスマートファクトリー化するメリット
工場をスマートファクトリー化すると、生産性の向上や技術承継の実現、設備管理の最適化といったメリットが得られます。現在、多くの製造業が抱えている課題の解消につながることが期待できます。
生産性の向上
スマートファクトリーでは、IoTを活用して製造工程に関わるさまざまなデータの収集・分析が可能です。各種データによって製造工程や進捗などを全体的に可視化できるため、ボトルネックになっている非効率な工程を特定できます。効率の悪い作業を特定し、作業分担などの改善策を検討・実施して効率化を図ることで、生産性の向上が期待できます。
技術継承の実現
スマートファクトリー化によって、工場内のあらゆるデータを収集して保存できるため、ベテラン従業員の熟練の技術を写真や動画、作業手順書などのデータに変換することが可能です。こうした技術の習得には、とかく長年の勘や経験といった“感覚頼み”になりがちですが、データ化することで、習得が難しいノウハウまで可視化でき、技術承継に役立てられます。人材育成に活用すれば、人手不足問題の改善にもつながります。
設備管理の最適化
スマートファクトリーでは、IoT活用によって在庫状況や作業の進捗、品質検査、機器の故障など、さまざまな情報がリアルタイムで確認できます。生産状況に応じて作業工程を最適化したり、機械や設備の故障時期を予測することが可能となります。
製品の製造に用いる機械以外にも、工場内の環境を管理するための空調や、機械に必要な電力を調節するエネルギー管理システムの調整なども自動で最適化されます。機械・設備の最適化により、品質の安定や生産性の向上、コスト削減などの実現にもつながります。
まとめ
日本の製造業は現在、人手不足をはじめさまざまな課題を抱えていますが、本記事で紹介したような、ICT化・スマートファクトリー化を推進することで、工場内のあらゆるデータが有効活用できるようになり、業務の自動化や効率化、設備の最適化からエネルギーコストの削減も期待できます。もし自社のビジネスの将来に不安があるのであれば、工場のICT化・スマートファクトリー化の検討をおすすめします。
製造業のスマートファクトリー化をデジタル技術から支援
日本の製造業は人材不足や老朽化した生産設備の維持、技能継承など、さまざまな問題を抱えており、これらに対応するため、生産性の向上が喫緊の課題となっています。NTT東日本は、「デジタル技術」と「セキュアなインフラ環境」によって、工場のデジタル化(スマートファクトリー化)をご支援。製造業の生産性向上をサポートします。
連載記事一覧
- 第1回 製造業におけるDX(デジタルトランスフォーメーション)の必要性とは?事例も合わせて紹介 2022.03.04 (Fri)
- 第2回 製造業における機械学習の事例および活用可能な機械学習技術について解説 2022.03.04 (Fri)
- 第3回 工場のスマートファクトリー化を進める課題とは何か 2022.03.04 (Fri)
- 第4回 ローカル5Gとは? 工場で導入する方法や事例を解説 2022.03.04 (Fri)
- 第5回 ファクトリーオートメーション(工場の自動化)とは?今後はどうなる? 2022.03.04 (Fri)
- 第6回 スマートファクトリーの土台となる工場のネットワークとは? 2022.03.04 (Fri)
- 第7回 ファクトリーオートメーションの事例や企業、今後とは? 2022.03.04 (Fri)
- 第8回 2021年6月より義務化! 食品事業者が知っておくべきHACCPの基本と事例を紹介 2022.03.04 (Fri)
- 第9回 製造業で注目を集めている「Anywhere Operations」とは?概要などについて解説 2022.03.04 (Fri)
- 第10回 製造業における情報セキュリティリスクの高まりとその対策方法 2022.03.04 (Fri)
- 第11回 製品開発のDX化のカギを握るCAE解析とは? 2022.03.04 (Fri)
- 第12回 製造業で導入が始まっているデジタルツインとは 2022.03.04 (Fri)
- 第13回 インダストリー4.0とは?概要や課題、事例などを紹介 2022.03.04 (Fri)
- 第14回 製造プロセスの最適化が期待できるPLMソリューションとは 2022.03.04 (Fri)
- 第16回 製造業を取り巻く現状と考えられる課題とは? その対策についても解説2023.01.30 (Mon)
- 第18回 工場を見える化するには? メリットや具体的な方法を紹介2023.01.30 (Mon)
- 第19回 製造業におけるヒューマンエラー対策とは? エラーが起こる原因も解説2023.01.30 (Mon)
- 第25回 製造業の今後は? 現状の課題や生き残るための手段を解説2023.01.30 (Mon)
- 第42回 事例から学ぶ、被害最大の「製造業」ランサムウェア対応2024.03.29 (Fri)
- 第43回 【用語解説】製造業が必ず押さえたい3つのセキュリティトレンド2024.03.29 (Fri)
- 第44回 工場停止で数千万の損害も、製造業に"すぐ必要"なサイバー攻撃対策とリスクアセスメント診断2024.03.29 (Fri)
- 第45回 自社だけ万全でも意味がない、サプライチェーン攻撃を防ぐには2024.03.29 (Fri)
- 第46回 ITとの違いから学ぶ、OTセキュリティ強化で知るべきポイント2024.03.29 (Fri)
- 第20回 製造業における品質管理の重要性とは? 品質対策のポイントも解説2023.01.30 (Mon)
- 第47回 突然、取引停止?工場セキュリティ未対策のリスク2024.03.29 (Fri)
- 第48回 OTセキュリティ強化の必読書、経産省発行のガイドラインを読み解く2024.03.29 (Fri)
- 第49回 製造業にも遵守義務、EUサイバーレジリエンス法とは?2024.03.29 (Fri)
- 第50回 ゼロからはじめる工場のセキュリティ対策2024.03.29 (Fri)
- 第21回 トレーサビリティとは? 種類や製造業におけるメリットを解説2023.01.30 (Mon)
- 第23回 工場に求められる安全対策とは?その重要性と対策のポイントを紹介2023.01.30 (Mon)
- 第50回 OTとITの融合を進めるために考えるべきこととは?2024.08.09 (Fri)
- 第51回 ニーズを捉えるための「多品種少量生産」とは?2024.08.09 (Fri)
- 第27回 工場を見える化することで得られるメリットは? 具体的な導入の流れも解説2023.01.30 (Mon)
- 第28回 工場の省人化とは? 実現するための具体的な方法を解説2023.01.30 (Mon)
- 第31回 生産管理とは? 目的や内容からシステムの選び方までわかりやすく解説2023.01.30 (Mon)
- 第32回 製造業の生産性を向上させるメリットやその際の着目ポイントなどを解説2023.01.30 (Mon)
- 第30回 製造業で品質向上をめざすには? 解決すべき課題について解説2023.01.30 (Mon)
- 第33回 生産管理が属人化する理由とは? 解消方法と標準化するメリットを解説2023.01.30 (Mon)
- 第35回 製造業におけるコスト削減のポイントとは? 具体例や今後の動向を解説2023.01.30 (Mon)
- 第37回 製造業における働き方改革とは? メリットや成功のポイントを解説2023.01.30 (Mon)
- 第36回 SCMとは? メリット・デメリットやERPとの違いについて解説2023.01.30 (Mon)
- 第38回 【製造業向け】RPA導入のメリットや注意点とは?2023.01.30 (Mon)
- 第29回 工場にAIを導入するメリット・デメリット、失敗するケースを解説2023.01.30 (Mon)
- 第34回 QCDとは? 生産管理の考え方やQCDの改善法について解説2023.01.30 (Mon)
- 第15回 工場の改善アイデア・事例5選! 業務改善を成功させるコツや実施手順も紹介2023.01.30 (Mon)
- 第17回 製造業のヒヤリハット事例5選 報告書の書き方や対策の進め方2023.01.30 (Mon)
- 第22回 製造業にIoTを導入するメリットとは? 事例や課題を解説2023.01.30 (Mon)
- 第24回 生産管理はAIでどう変わる? 製造業におけるAIの活用事例を紹介2023.01.30 (Mon)
- 第26回 工場は深刻な人手不足。その原因と5つの対策法とは2023.01.30 (Mon)
- 第39回 増えている製造業へのサイバー攻撃! 理由や対策法を徹底解説2023.02.15 (Wed)
- 第40回 工場の現場をペーパーレス化するメリットとは? 導入ステップやツールを紹介2023.02.15 (Wed)
- 第41回 多能工化とは何か? メリット・デメリットと失敗しない進め方を解説2023.02.15 (Wed)