2023.01.30 (Mon)
ICTで製造業はどのように変わるのか(第23回)
工場に求められる安全対策とは?その重要性と対策のポイントを紹介
工場の現場では日々多くの機械が稼動しているため、安全対策が必須といえる環境です。厚生労働省の調査では、令和3年の労働災害による死亡事故が前年より増加しており、企業はさらなる安全対策が求められています。
本記事では、工場における安全対策の重要性やよくある事故の種類、工場が行うべき対策である「5S活動」や「KYT活動」、「ヒヤリハット活動」の概要や効果、取り組む際のポイントを解説します。
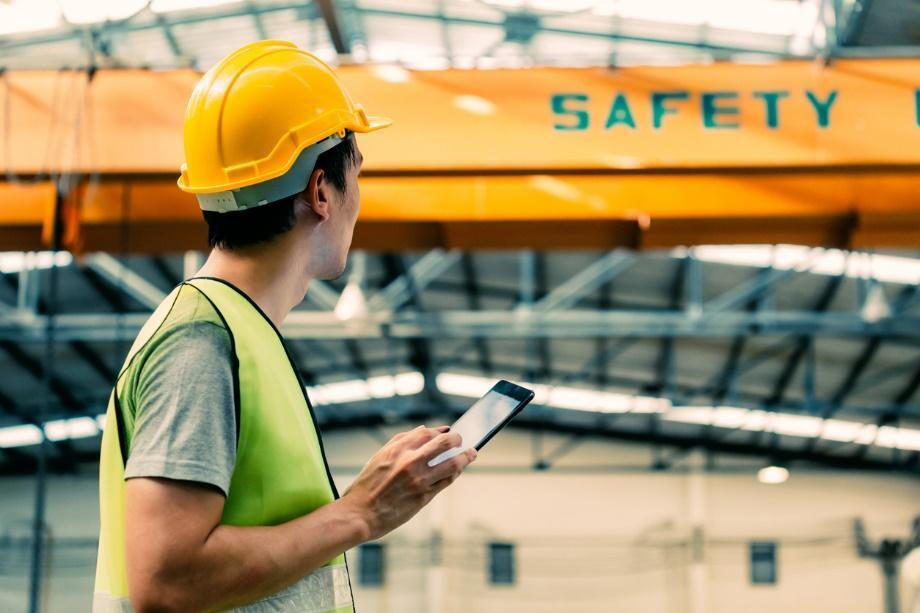
工場における安全対策の重要性
工場や作業現場における事故は現在も発生しており、怪我人だけでなく死亡者も出ています。
厚生労働省が発表した「令和3年労働災害発生状況の分析等」によると、令和3年に起こった労働災害による死亡者数は、全産業で867人でした。平成29年度に比べ111人減っていますが、前年度の802人と比較すると、65人も増えています。
厚生労働省は労働災害の減少を目的として、5年単位で取りまとめる中期計画「13次労働災害防止計画」を掲げており、令和4年までに死亡災害を5年前より15%以上減少させることを目標としていました。しかし、令和3年度の結果から平成29年度を比較すると、減少の割合はマイナス11.3%にとどまっています。
同計画で死亡災害の重点業種と定めてられている製造業と建設業、林業では、平成29年と比較して、それぞれマイナス10~25%程減少しました。しかし、前年度の令和2年と比べると、製造業ではプラス0.7%、建設業ではプラス11.6%と、増加に転じています。
工場では常にさまざまな機械が稼動し、化学物質などの危険物や重量のある資材などを扱っています。そのような中で安全対策を怠ると、重大な事故を引き起こしかねません。労働災害を減らすため、工場を有する企業にはさらなる安全対策の強化が求められています。
工場でよくある事故の種類
多様な機械や物を扱う工場では、事故の種類もさまざまです。ここでは厚生労働省による「令和3年労働災害発生状況の分析等」を参考に、工場で起こりやすい事故を解説します。
はさまれ・巻き込まれ
はさまれ・巻き込まれ事故は、令和3年度の死傷者数(休業4日以上)が全業種で14,020人と多発しています。技術革新により機械の安全性が向上したものの、注意不足による事故はゼロにはなりません。製造業では特に多発しており、令和3年には54人の死亡者も出ています。
「はさまれ」は、機械の可動部分に身体の一部がはさまれて起こる事故で、「巻き込まれ」は、身体の一部が巻き込まれる事故です。特に機械のメンテナンス中に起こりやすく、ある飲料缶製造工場では、ボルトの緩み点検・締め付け作業中の従業員が機械に挟まれて死亡したという事例もあります。これ以外にも、工場内を手押し式掃除機で清掃中に、前進してきたフォークリフトに轢かれ、大腿骨骨折という重傷を負ったという事例もあり、これもはさまれ・巻き込まれ事故に含まれます。
転倒
令和3年における事故の型別死傷者数(休業4日以上)において、全業種33,672人と一番多かったのが、転倒事故による死傷者数です。何かを運搬中にバランスを崩して転倒したり、作業中に足元の突起物につまずき転倒したりと、機械や物が多くある工場では特に起こりやすくなります。もちろん軽症で済めばよいですが、転倒した先に危険物がある場合は、重大な怪我を負ったり、最悪の場合は死亡に至るケースもあります。
従業員自身の転倒だけでなく、機器が転倒することも、転倒事故に含まれます。たとえばフォークリフトと運搬台車がぶつかりそうになり、フォークリフトが急ハンドルを切ったため横転、運転者はフォークリフトの倒れた方向に飛び降りてしまったため、下敷きとなってしまった、という事故も発生しています。
墜落・転落
工場では、はしごや脚立、リフト、クレーンを使った高所作業の際に転落する「墜落・転落」事故の労働災害も多い傾向があります。令和3年は全業種において、死傷者数(休業4日以上)が21,286人発生しており、製造業では令和3年に25人が亡くなっています。
脚立のぐらつきなどで転落する事故も多いですが、なかには天井クレーンのメンテナンス中に約20m下の床に転落し、死亡する事例もあります。
切れ・こすれ
工場では、切れ・こすれの事故も比較的多いです。令和3年の全業種における死傷者数(休業4日以上)は、切れ・こすれによって7,638人の死傷者数が出ています。業務用カッターやスライサー、電動丸のこなどに接触し、指を切ったり、切断するなどの労働災害が該当します。
切れ・こすれによる死亡事故も発生しています。たとえばある工場で、従業員が単独で角材を加工する作業を行っていたところ、丸のこの歯が大腿部に接触。発見が遅れたため、出血多量等で死亡する労働災害が起きました。
工場における安全対策 [その1]5S
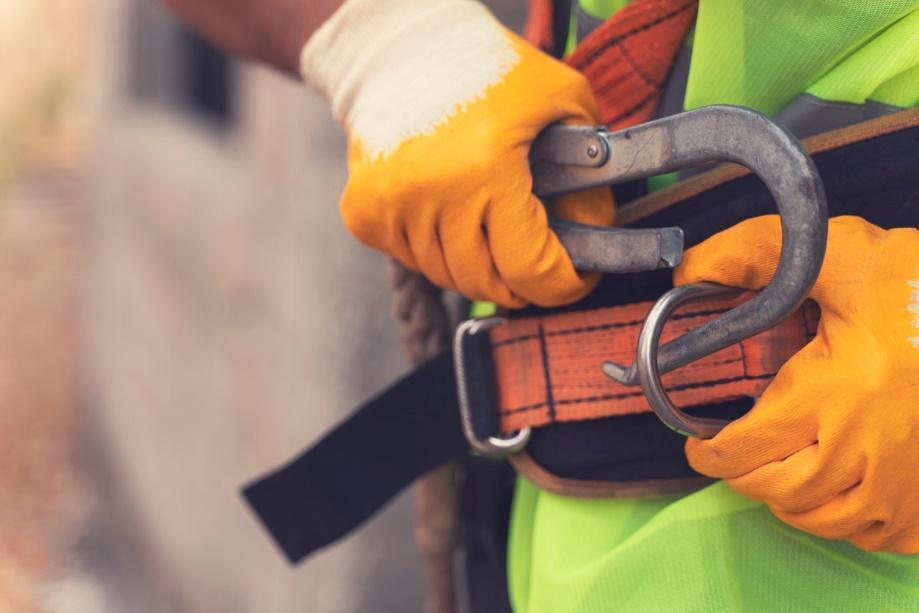
工場や作業場において労働災害を起こさないためには、安全対策の徹底が重要です。もっとも一般的な対策のひとつが「5S」です。
5Sとは
5Sとは、安全対策の改善や職場環境を整えるためにつくられたスローガンです。整理(Seiri)、整頓(Seiton)、清掃(Seisou)、清潔(Seiketsu)、しつけ(Shitsuke)をローマ字にしてそれぞれの頭文字「S」を取ったものです。
これらの単語は英単語にしても頭文字が「S」になり(Sort、Set、Shine、Standardize 、Sustain)、日本のみならず、世界的に利用されているスローガンです。この「5S」に取り組む活動のことを「5S活動」といいます。
5Sで期待できる効果
5Sには、労働災害を起こさないための重要な要素が含まれています。職場が「整理」されていれば転倒が防止でき、資材や道具が「整頓」されていれば、事故に発展する恐れのある危険物に気づけます。さらに、転倒だけでなく転落事故を防ぐためにも、作業場所の「清掃」「清潔」は欠かせません。
加えて、従業員に労働災害の危険性や、それを起こさない取り組みの必要性を認識するよう「しつけ」を行なうことで、工場の安全対策を向上できます。
5Sは業務効率化にも効果的です。職場が整理整頓され、掃除が定期的に行われている清潔な職場では、業務に必要な道具も見つけやすく、それを探す無駄な時間が削減できます。従業員も気持ちよく働くことができ、業務効率も向上するでしょう。
5Sに取り組むときのポイント
5S活動に取り組む際には、押さえるべきポイントがあります。そのひとつは「活動目的の明確化」です。目的が明確でないと、従業員の理解が得られず、うやむやになる恐れがあるからです。
さらに、目的に向かって共通認識をもつことも重要です。従業員が、「ただやらされている」というような受け身の状況では、5S活動は実を結びません。従業員に対し、5S活動についての意見を募集したり、ルール策定に参加を促すなどの工夫も必要です。
工場における安全対策 [その2]KYT(危険予知トレーニング)
工場における安全対策に有効な手段として「KYT(危険予知トレーニング)」というものがあります。
KYTとは
KYTは、危険(Kiken)予知(Yochi)トレーニング(Traning)の頭文字から名づけられた言葉です。KYTでは、従業員みずから職場や作業中に潜む危険要因に対して感受性を高め、その問題を解決する能力を向上させるための訓練を行います。
KYTには「4ラウンド法」という手法があり、1Rから4Rまでの段階に沿って進めていきます。1Rは、どのような危険が潜んでいるかなどの「現状把握」の段階です。まず危険だと思われる現象をすべて挙げていきます。2Rでは、挙げられた危険要因から重要度を分類する「本質追求」です。続く3Rでは、2Rで認識された危険ポイントに対する具体策を立てる「対策樹立」を実施します。最後の4Rでは、3Rで挙げられた具体策について行動目標を掲げる「目標設定」を行います。
KYTで期待できる効果
KYTを行うことで、ヒューマンエラーやリスクテイキング(リスクを認識しながら行動すること)を起こす心理状態を把握できます。さらに、安全を自分自身の問題として認識できるようになり、危険予知能力が向上します。通常の作業や行動も注意深くなり、最終的には労働災害の防止につながります。
一方で、KYTは安全対策だけではなく、チームワークの向上やリーダーシップ能力の育成、良い職場風土を醸成できるなどの効果もあります。これにより、安全面の話し合いや助け合いも気軽にできる環境が形づくられ、安全対策もより効果的なものになります。
KYTに取り組むときのポイント
KYTに取り組む際には、ラウンドごとに押さえるべきポイントがあります。まず1Rにおける「現状把握」では、過去の事例にこだわらず、今起こり得る危険を挙げていくことが重要です。2Rの「本質追求」では、多数決ではなく、メンバー全員の意見を反映することが求められます。意見が一致するまで、メンバー同士で話し合うことが大切です。3Rの「対策樹立」では普段の業務で実践可能な具体策を立てることが、4Rの「目標設定」では設定した目標を掲示板に掲出するなど、チーム全体で共通認識をもつことが重要になります。
工場における安全対策 [その3] ヒヤリハット活動
工場における安全対策では、「ヒヤリハット活動」も効果をもたらします。
ヒヤリハット活動とは
ヒヤリハットとは、その名の通り「ヒヤリとした」または「ハッとした」という言葉を掛け合わせたもので、ひとつ間違えば重大な事故になりかねないとされる出来事を示します。ヒヤリハット事例を発見し、集めて対策を立てることが「ヒヤリハット活動」です。
ヒヤリハットは、焦りや油断などのメンタル面から来るものや、情報の共有不足、5Sが徹底されていないケースで起きやすいとされています。
ヒヤリハット活動で期待できる効果
ヒヤリハット活動によって、重大な事故を防ぐ効果が期待できます。
1931年にアメリカの損害保険会社に勤務していたハーバード・ウィリアム・ハインリッヒ氏が導き出した「ハインリッヒの法則」(1:29:300の法則)によると、同じ人間が起こした330件うち1件は重い災害があったとした場合、29回の軽傷、300回の障害のない事故を起こしているといいます。つまり、膨大なヒヤリハットの中には、1件の重大事故が起きる恐れがあるともいえます。つまり、ヒヤリハット活動によって細かなヒヤリハット事例が起きるのを防ぐことで、1件の重大事故が防げることになります。
ヒヤリハット活動に取り組むときのポイント
効果の高いヒヤリハット活動を行うには、「速やかな報告書作成」、「原因の明確化」、「対策の周知」が重要です。
「速やかな報告書作成」については、ヒヤリハットを経験してから時間が経つと、経緯が曖昧になってしまう恐れがあるため、記憶が鮮明なうちに報告書を作成する必要があります。
「原因の明確化」を行う理由は、単に報告書を作成しただけでは、ヒヤリハットが無くならないからです。原因を分析し、明確化することで、再発防止に役立てられます。
最後に「対策の周知」を行います。対策を練る際には、作業を行う従業員からも案を集め、有効な対策を決定した後は、掲示板に貼るなど周知を行います。
まとめ
工場や作業場では、少しのミスが大きな事故に発展する危険性を秘めています。事故を1件でも減らすための対策や注意喚起の徹底は、重要な課題です。今回の記事で取り上げた、5S、KYT、ヒヤリハット活動といった取り組みを進めることで、事故の発生を抑え、安全に業務を行っていくことが可能になります。
NTT東日本では、デジタル技術とネットワーク構築によるスマートファクトリー化で製造業の生産性向上を支援しています。生産機器の異変を事前に察知したり、無人での自動搬入を実現するなど、デジタルの面から工場の安全性を高めることが可能です。サービスについて詳しく知りたい方は、ぜひ下記をご覧ください。
製造業のスマートファクトリー化をデジタル技術から支援
日本の製造業は人材不足や老朽化した生産設備の維持、技能継承など、さまざまな問題を抱えており、これらに対応するため、生産性の向上が喫緊の課題となっています。NTT東日本は、「デジタル技術」と「セキュアなインフラ環境」によって、工場のデジタル化(スマートファクトリー化)をご支援。製造業の生産性向上をサポートします。
連載記事一覧
- 第1回 製造業におけるDX(デジタルトランスフォーメーション)の必要性とは?事例も合わせて紹介 2022.03.04 (Fri)
- 第2回 製造業における機械学習の事例および活用可能な機械学習技術について解説 2022.03.04 (Fri)
- 第3回 工場のスマートファクトリー化を進める課題とは何か 2022.03.04 (Fri)
- 第4回 ローカル5Gとは? 工場で導入する方法や事例を解説 2022.03.04 (Fri)
- 第5回 ファクトリーオートメーション(工場の自動化)とは?今後はどうなる? 2022.03.04 (Fri)
- 第6回 スマートファクトリーの土台となる工場のネットワークとは? 2022.03.04 (Fri)
- 第7回 ファクトリーオートメーションの事例や企業、今後とは? 2022.03.04 (Fri)
- 第8回 2021年6月より義務化! 食品事業者が知っておくべきHACCPの基本と事例を紹介 2022.03.04 (Fri)
- 第9回 製造業で注目を集めている「Anywhere Operations」とは?概要などについて解説 2022.03.04 (Fri)
- 第10回 製造業における情報セキュリティリスクの高まりとその対策方法 2022.03.04 (Fri)
- 第11回 製品開発のDX化のカギを握るCAE解析とは? 2022.03.04 (Fri)
- 第12回 製造業で導入が始まっているデジタルツインとは 2022.03.04 (Fri)
- 第13回 インダストリー4.0とは?概要や課題、事例などを紹介 2022.03.04 (Fri)
- 第14回 製造プロセスの最適化が期待できるPLMソリューションとは 2022.03.04 (Fri)
- 第16回 製造業を取り巻く現状と考えられる課題とは? その対策についても解説2023.01.30 (Mon)
- 第18回 工場を見える化するには? メリットや具体的な方法を紹介2023.01.30 (Mon)
- 第19回 製造業におけるヒューマンエラー対策とは? エラーが起こる原因も解説2023.01.30 (Mon)
- 第25回 製造業の今後は? 現状の課題や生き残るための手段を解説2023.01.30 (Mon)
- 第42回 事例から学ぶ、被害最大の「製造業」ランサムウェア対応2024.03.29 (Fri)
- 第43回 【用語解説】製造業が必ず押さえたい3つのセキュリティトレンド2024.03.29 (Fri)
- 第44回 工場停止で数千万の損害も、製造業に"すぐ必要"なサイバー攻撃対策とリスクアセスメント診断2024.03.29 (Fri)
- 第45回 自社だけ万全でも意味がない、サプライチェーン攻撃を防ぐには2024.03.29 (Fri)
- 第46回 ITとの違いから学ぶ、OTセキュリティ強化で知るべきポイント2024.03.29 (Fri)
- 第20回 製造業における品質管理の重要性とは? 品質対策のポイントも解説2023.01.30 (Mon)
- 第47回 突然、取引停止?工場セキュリティ未対策のリスク2024.03.29 (Fri)
- 第48回 OTセキュリティ強化の必読書、経産省発行のガイドラインを読み解く2024.03.29 (Fri)
- 第49回 製造業にも遵守義務、EUサイバーレジリエンス法とは?2024.03.29 (Fri)
- 第50回 ゼロからはじめる工場のセキュリティ対策2024.03.29 (Fri)
- 第21回 トレーサビリティとは? 種類や製造業におけるメリットを解説2023.01.30 (Mon)
- 第23回 工場に求められる安全対策とは?その重要性と対策のポイントを紹介2023.01.30 (Mon)
- 第50回 OTとITの融合を進めるために考えるべきこととは?2024.08.09 (Fri)
- 第51回 ニーズを捉えるための「多品種少量生産」とは?2024.08.09 (Fri)
- 第27回 工場を見える化することで得られるメリットは? 具体的な導入の流れも解説2023.01.30 (Mon)
- 第28回 工場の省人化とは? 実現するための具体的な方法を解説2023.01.30 (Mon)
- 第31回 生産管理とは? 目的や内容からシステムの選び方までわかりやすく解説2023.01.30 (Mon)
- 第32回 製造業の生産性を向上させるメリットやその際の着目ポイントなどを解説2023.01.30 (Mon)
- 第30回 製造業で品質向上をめざすには? 解決すべき課題について解説2023.01.30 (Mon)
- 第33回 生産管理が属人化する理由とは? 解消方法と標準化するメリットを解説2023.01.30 (Mon)
- 第35回 製造業におけるコスト削減のポイントとは? 具体例や今後の動向を解説2023.01.30 (Mon)
- 第37回 製造業における働き方改革とは? メリットや成功のポイントを解説2023.01.30 (Mon)
- 第36回 SCMとは? メリット・デメリットやERPとの違いについて解説2023.01.30 (Mon)
- 第38回 【製造業向け】RPA導入のメリットや注意点とは?2023.01.30 (Mon)
- 第29回 工場にAIを導入するメリット・デメリット、失敗するケースを解説2023.01.30 (Mon)
- 第34回 QCDとは? 生産管理の考え方やQCDの改善法について解説2023.01.30 (Mon)
- 第15回 工場の改善アイデア・事例5選! 業務改善を成功させるコツや実施手順も紹介2023.01.30 (Mon)
- 第17回 製造業のヒヤリハット事例5選 報告書の書き方や対策の進め方2023.01.30 (Mon)
- 第22回 製造業にIoTを導入するメリットとは? 事例や課題を解説2023.01.30 (Mon)
- 第24回 生産管理はAIでどう変わる? 製造業におけるAIの活用事例を紹介2023.01.30 (Mon)
- 第26回 工場は深刻な人手不足。その原因と5つの対策法とは2023.01.30 (Mon)
- 第39回 増えている製造業へのサイバー攻撃! 理由や対策法を徹底解説2023.02.15 (Wed)
- 第40回 工場の現場をペーパーレス化するメリットとは? 導入ステップやツールを紹介2023.02.15 (Wed)
- 第41回 多能工化とは何か? メリット・デメリットと失敗しない進め方を解説2023.02.15 (Wed)