2023.01.30 (Mon)
ICTで製造業はどのように変わるのか(第20回)
製造業における品質管理の重要性とは? 品質対策のポイントも解説
製造業において品質管理は、完成した製品の品質を維持するために欠かせない業務です。企業が製造・販売する製品には、それぞれ独自の品質基準が定められています。しかし、定められた品質基準を満たし、適切な管理を実施するためには、解決すべき課題が多くあります。この記事では、製造業における品質管理の重要性とともに、品質管理を構成する3つの要素や解決すべき課題、改善ポイントなどを解説します。
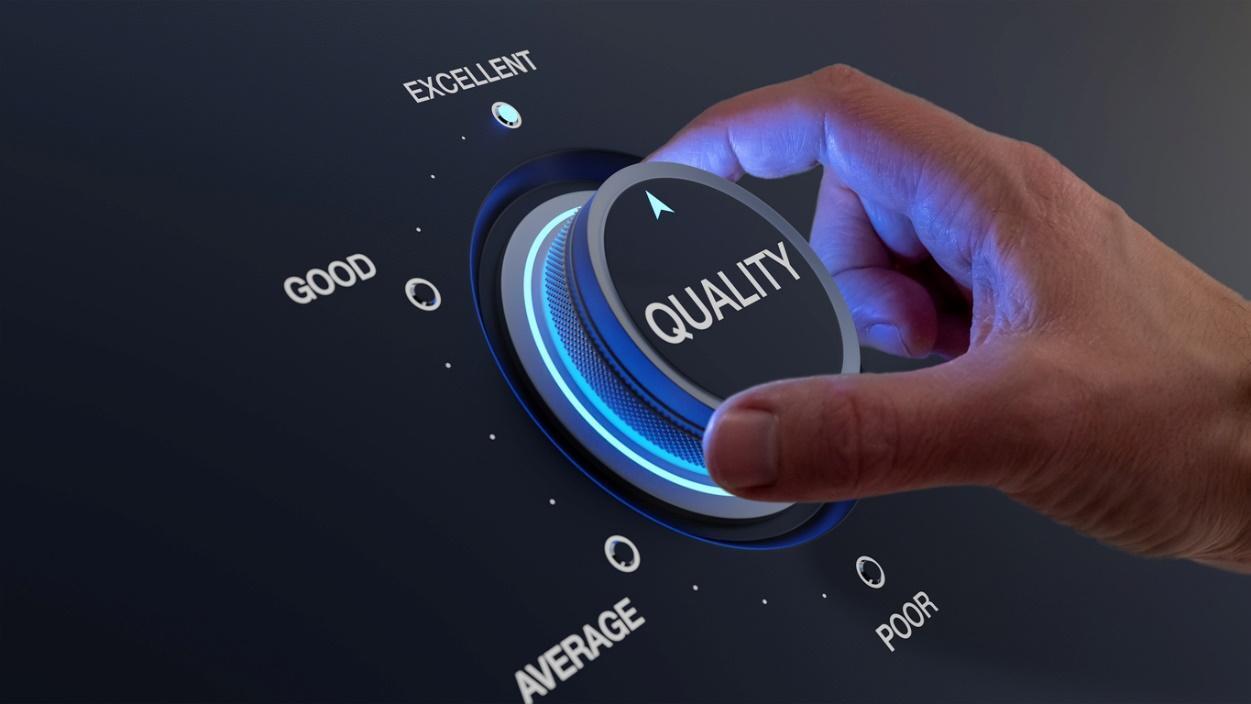
製造業の品質管理とは?
製造業の品質管理とは、製品を製造する際に一定の品質が保たれているか、不良品が混ざっていないかなどを検査・検証し管理する業務のことです。英語では「Quality Control(クオリティ・コントロール)」「QC」とも呼ばれています。品質管理を行うことによって、製造業の現場から市場に向けて品質の安定した製品を提供することが可能になるのです。
製造品質管理では、製品の日常的な点検業務や修理・交換に加えて、不良品を発見したとき、原因と発生過程を確認することが大切です。原因と発生過程を確認しないと、有効な再発防止策がとれないからです。このほか企業が定める品質を維持するために、正しい作業手順の設定、手順通りに製品を製造できる環境の構築、製造技術を持つ人材の育成といった業務も行われます。
品質管理の重要性
もし品質管理を行わないとしたら、低品質の製品や不良品をそのまま販売することになります。結果、購入者からのクレームが増加して、自社製品や企業への信用が低下する恐れがあります。
不良品によって不利益を被るのは、企業だけではありません。不良品を手にした購入者が怪我をする可能性も否めません。万が一の場合、不良品が原因で火事や交通事故などの重大事故が発生して、不特定多数の人々へ危害を与えてしまうこともあるでしょう。
不良品が原因で事故が発生した場合、損害賠償の支払いが発生するなど、経営継続に影響を与える事態に陥ることも考えられます。これらのトラブルを回避し、安定した品質の製品を提供するためには、適切な品質管理が不可欠なのです。
適切な品質管理によって、不良品が出荷されるトラブルを防ぎ、安心して使用できる製品を提供できれば、企業としての実績が認められ、信頼性や顧客満足度が向上します。製品・企業への信頼性が高まることで、新規顧客獲得やリピーターの増加による売上アップ、長期間の経営継続も期待できます。
品質管理を構成する3つの要素
品質管理は、大きく分けて「工程管理」「品質検証」「品質改善」の3要素から構成されます。ここでは、それぞれの要素の概要と、製造段階に応じた管理方法について解説します。
工程管理
工程管理は、製品を製造する作業工程を適切に管理する業務です。
作業手順や作業工程が工場や従業員により異なると、不良品が発生する確率が高まるため、マニュアル作成などにより作業工程を標準化する必要があります。工程管理では日々の工程から稼働状況、製品の品質といった管理に必要な数値を記録して、管理図を作ることが必要です。
従業員の技術力に個人差があると、製品の仕上がりにばらつきが生じます。従業員が作業を適切に行える一定の技術力を得るためには、従業員の作業訓練や知識の習得など、教育面も意識する必要があります。
製造に使用する設備は、維持や管理を行わなければいけません。設備は、摩耗や経年による劣化が生じます。そのため、定期的に点検し、必要に応じて修理や交換を行います。このように、作業工程を技術面や設備面などから最適化することで、作業ミスの発生を防止して、製品の品質向上や作業効率化につなげます。
品質検証
品質検証は、製品の品質や機能に問題がないかを検証する業務です。製品の原材料や部品の受け入れ時には「受け入れ検査」、各製造工程では「工程内検査」、製品の完成時には「完成品検査」、倉庫に保管していた製品の出荷時には「出荷検査」と、要所で必要な品質検証を実施します。
完成品検査では、製品の強度・耐久性を確認する「破壊検査」や、破壊せずに製品サンプルを調べる「非破壊検査」を実施して、完成品の質を検証・保証します。品質基準の判断に用いられるのは、日本産業規格(JIS)や国際規格(ISO規格)などです。
受け入れ検査・工程内検査・完成品検査などは、工程能力の監視を目的として行われます。その際は、CpやCpk(「定められた規定値の中で、製品のデータにどれだけばらつきがあるのか」を数値化したもの。Cはが理想的に管理された工程を、Cpkはある程度の偏りが発生する、より実務的な工程を想定している)といった「工程能力指数」を用いて、検査製造工程に成果物の質を低下させる原因がないかを検証します。
品質改善
品質改善は、不良品の発生予防および再発防止のために改善を行う業務です。不良品の再発を防ぐためには、「QCストーリー」と呼ばれる問題改善に用いるプロセスを使用します。QCストーリーは、不良品が生じた原因を調べるためにデータ収集して現状を把握し、原因を分析して対策を講じ、解決していく手法です。
不良品を未然に防ぐためには、「工程FMEA」などの手法が用いられます。FMEAとは「Failure Mode and Effect Analysis」の略で、日本語では「故障モード影響解析」と呼ばれています。製造プロセスで生じる恐れのあるさまざまな要因を洗い出し、不良品発生の予防を図る手法です。
製造業の品質管理における課題
製造業の品質管理を適切に行うためには、人手不足や部門間の連携不足、現場での施策未実施などの過大を解決する必要があります。
人手不足
日本では少子化による人口減少などの影響により、人手不足に悩む企業が増加しており、製造業は特にその傾向が顕著に見られます。経済産業省・厚生労働省・文部科学省が発行した「2022年版ものづくり白書」によると、2002年度における製造業の若年就業者数は約384万人だったのに対し、2021年度では約263万人と、20年間で約120万人も減少しています。
品質管理の観点からすると。人手不足により従業員の業務負担が増加し、品質管理業務に人手を回すことが難しくなる可能性が懸念されています。
近年は、熟練の技術者から次の世代へと技術を引き継ぐ、いわゆる技術継承が行われないケースも耳にします。若い技術者への技術継承が行われなければ業務の属人化につながり、熟練技術者が退職した際、品質低下を招きかねません。
部門間の連携が不十分
製造業では、製品製造の工程が各部門で分かれているため、部門間の連携が取りにくい点も課題のひとつです。製品の製造には、営業部・開発部・製造部などさまざまな部門が関係しています。部門間の連携が十分に取れていないと、製造現場の現状や基準としている品質レベル、顧客のニーズまで、品質・生産管理における重要な点が共有できません。
各部門のデータがほかの部門と共有されないと、「営業部が保有する顧客ニーズに関するデータを、開発部や製造部が把握できない」といったデメリットが生じます。データが紙媒体で保存されていたり、部門ごとに独自のExcelファイルで管理している場合も、他部門との情報共有が難しくなります。
実施した施策が現場に定着しない
品質向上のために現状分析を行い、改善施策を実施したところで、施策内容が現場の状況に適していなければ、定着は難しいでしょう。いくら不良品発生の原因を把握し、改善に向けた施策を策定しても、現場で活用されなければ意味がありません。改善施策を定着させるには、現場の状況をよく知り、実態に即した施策を取り入れることが大切です。
製造業で品質管理を改善するポイント
製造業で品質管理を改善するには、いくつかのポイントを押さえる必要があります。具体的には「5S」の定着や「4M」の管理、手順書の整備、PDCAサイクルを回す、DX促進を実施するなどの方法が挙げられます。
現場に5Sを定着させる
5Sとは、「整理」「整頓」「清掃」「清潔」「しつけ」の頭文字Sから始まる5要素からなる、工程管理でよく用いられる手法です。それぞれ次のような意味があります。
【5Sの意味】
・整理:工具など、いる物といらない物を分けて、不要な物を処分すること。
・整頓:必要な物をきれいに並べて作業しやすくすること。
・清掃:使った物をきれいに掃除し、すぐ使えるように点検すること。
・清潔:清掃によりきれいな状態を維持すること。
・しつけ:上記4つを継続するために職場のルールをつくり、習慣づけること。
製造ラインでは、この5Sに基づき工具の整理整頓などを管理する方法やルールを設定します。5Sを徹底することで、現場で作業しやすい最適な環境を維持でき、作業ミスや作業時の無駄をなくして業務効率化につなげられます。
4Mを管理する
4Mとは、「人(Man)」「設備(Machine)」「方法(Method)」「材料(Material)」の4つの言葉からつくられた品質管理手法です。それぞれ製造ラインを構成する4つの要素を表し、これらをベースに分析することで、不良品が生じた場合もスピーディに原因を特定しやすくなります。
【4Mの意味】
・人(Man):現場の従業員のこと。各従業員のスキルや適性を分析し、適正な配置が行われているかなどを管理します。資格制度によるスキルアップの促進も効果的です。
・設備(Machine):工場の機械設備のこと。メンテナンスや点検を実施しているか、最新設備の導入を検討すべきかなどを管理します。
・方法(Method):正しい作業手順で製造を徹底すること。品質管理の各製造工程を標準化し、マニュアルを作成しているかなどを管理します。
・材料(Material):製品の原材料や部品のこと。これらに欠陥や不良品がなく、基準を満たしているかなどを管理します。
手順書を整備し、業務標準化を図る
品質管理に大きく影響するのが、業務属人化による作業手順のばらつきです。作業者によって手順が異なってしまうと、品質の低下を招きやすい傾向があります。作業手順にばらつきが生じている場合は、適切な業務プロセスをまとめた手順書の整備によって業務標準化を図ることが重要です。
PDCAサイクルを回す
PDCAサイクルとは、「計画(Plan)」→「実行(Do)」→「評価(Check)」→「改善(Action)」の4工程で業務改善を目指す手法です。
「計画」の工程では目標を設定し、計画を立てます。「実行」の工程では、立案した目標に向けて計画を実行します。「評価」の工程では、実行した内容が計画通りできているか確認し、成功もしくは失敗した原因の検証・分析を行います。最後の「処理」の工程は、分析した結果に基づき改善策を立案・実施します。
PDCAの順番で行われるサイクルは、基本的に一度だけでは完了しません。サイクルを何度も繰り返し回すことで、継続的な改善を図るのがポイントです。
DXを推進する

DX(デジタルトランスフォーメーション)を推進することも、品質管理の改善につながります。DXは、ICTを活用し、業務全体を変化させる取り組みのことです。ICT化により製品の原材料から作業工程、責任者まですべての情報をデータで管理し、すぐに情報を確認できる環境なども構築できます。万一、問題が生じた際には、保存データを原因の特定に役立てることが可能です。
近年の品質管理では、AIソリューションの導入も注目を集めています。AIソリューションは、人の目では検知が難しい部分も異常を検知できるため、外観検査の自動化などをはじめ、幅広い検査での活用が期待されています。DXの推進により、データ管理の最適化や業務自動化による正確性の向上、作業の標準化、人材不足の解消などさまざまなメリットが期待できます。
まとめ
製造業の品質管理は、製品の品質を保つ目的や、不良品の原因を特定して再発防止に役立てるなどの目的で行われます。不良品の製造・提供は、クレームだけでなく事故の発生につながるおそれもあるため、品質管理を徹底して未然に防止する必要があります。
製造業の品質管理では、人手不足をはじめさまざまな課題が浮き彫りとなっていますが、DXの推進によりそれら課題を解決しつつ、大幅な業務効率化が期待できます。NTT東日本では、生産状況の把握やカメラ・センサーなどによる検品の効率化など、DXの推進による製造業の生産性向上を支援しています。DX化を検討中の方は、下記をぜひ参考にしてください。
製造業のスマートファクトリー化をデジタル技術から支援
日本の製造業は人材不足や老朽化した生産設備の維持、技能継承など、さまざまな問題を抱えており、これらに対応するため、生産性の向上が喫緊の課題となっています。NTT東日本は、「デジタル技術」と「セキュアなインフラ環境」によって、工場のデジタル化(スマートファクトリー化)をご支援。製造業の生産性向上をサポートします。
連載記事一覧
- 第1回 製造業におけるDX(デジタルトランスフォーメーション)の必要性とは?事例も合わせて紹介 2022.03.04 (Fri)
- 第2回 製造業における機械学習の事例および活用可能な機械学習技術について解説 2022.03.04 (Fri)
- 第3回 工場のスマートファクトリー化を進める課題とは何か 2022.03.04 (Fri)
- 第4回 ローカル5Gとは? 工場で導入する方法や事例を解説 2022.03.04 (Fri)
- 第5回 ファクトリーオートメーション(工場の自動化)とは?今後はどうなる? 2022.03.04 (Fri)
- 第6回 スマートファクトリーの土台となる工場のネットワークとは? 2022.03.04 (Fri)
- 第7回 ファクトリーオートメーションの事例や企業、今後とは? 2022.03.04 (Fri)
- 第8回 2021年6月より義務化! 食品事業者が知っておくべきHACCPの基本と事例を紹介 2022.03.04 (Fri)
- 第9回 製造業で注目を集めている「Anywhere Operations」とは?概要などについて解説 2022.03.04 (Fri)
- 第10回 製造業における情報セキュリティリスクの高まりとその対策方法 2022.03.04 (Fri)
- 第11回 製品開発のDX化のカギを握るCAE解析とは? 2022.03.04 (Fri)
- 第12回 製造業で導入が始まっているデジタルツインとは 2022.03.04 (Fri)
- 第13回 インダストリー4.0とは?概要や課題、事例などを紹介 2022.03.04 (Fri)
- 第14回 製造プロセスの最適化が期待できるPLMソリューションとは 2022.03.04 (Fri)
- 第16回 製造業を取り巻く現状と考えられる課題とは? その対策についても解説2023.01.30 (Mon)
- 第18回 工場を見える化するには? メリットや具体的な方法を紹介2023.01.30 (Mon)
- 第19回 製造業におけるヒューマンエラー対策とは? エラーが起こる原因も解説2023.01.30 (Mon)
- 第25回 製造業の今後は? 現状の課題や生き残るための手段を解説2023.01.30 (Mon)
- 第42回 事例から学ぶ、被害最大の「製造業」ランサムウェア対応2024.03.29 (Fri)
- 第43回 【用語解説】製造業が必ず押さえたい3つのセキュリティトレンド2024.03.29 (Fri)
- 第44回 工場停止で数千万の損害も、製造業に"すぐ必要"なサイバー攻撃対策とリスクアセスメント診断2024.03.29 (Fri)
- 第45回 自社だけ万全でも意味がない、サプライチェーン攻撃を防ぐには2024.03.29 (Fri)
- 第46回 ITとの違いから学ぶ、OTセキュリティ強化で知るべきポイント2024.03.29 (Fri)
- 第20回 製造業における品質管理の重要性とは? 品質対策のポイントも解説2023.01.30 (Mon)
- 第47回 突然、取引停止?工場セキュリティ未対策のリスク2024.03.29 (Fri)
- 第48回 OTセキュリティ強化の必読書、経産省発行のガイドラインを読み解く2024.03.29 (Fri)
- 第49回 製造業にも遵守義務、EUサイバーレジリエンス法とは?2024.03.29 (Fri)
- 第50回 ゼロからはじめる工場のセキュリティ対策2024.03.29 (Fri)
- 第21回 トレーサビリティとは? 種類や製造業におけるメリットを解説2023.01.30 (Mon)
- 第23回 工場に求められる安全対策とは?その重要性と対策のポイントを紹介2023.01.30 (Mon)
- 第50回 OTとITの融合を進めるために考えるべきこととは?2024.08.09 (Fri)
- 第51回 ニーズを捉えるための「多品種少量生産」とは?2024.08.09 (Fri)
- 第27回 工場を見える化することで得られるメリットは? 具体的な導入の流れも解説2023.01.30 (Mon)
- 第28回 工場の省人化とは? 実現するための具体的な方法を解説2023.01.30 (Mon)
- 第31回 生産管理とは? 目的や内容からシステムの選び方までわかりやすく解説2023.01.30 (Mon)
- 第32回 製造業の生産性を向上させるメリットやその際の着目ポイントなどを解説2023.01.30 (Mon)
- 第30回 製造業で品質向上をめざすには? 解決すべき課題について解説2023.01.30 (Mon)
- 第33回 生産管理が属人化する理由とは? 解消方法と標準化するメリットを解説2023.01.30 (Mon)
- 第35回 製造業におけるコスト削減のポイントとは? 具体例や今後の動向を解説2023.01.30 (Mon)
- 第37回 製造業における働き方改革とは? メリットや成功のポイントを解説2023.01.30 (Mon)
- 第36回 SCMとは? メリット・デメリットやERPとの違いについて解説2023.01.30 (Mon)
- 第38回 【製造業向け】RPA導入のメリットや注意点とは?2023.01.30 (Mon)
- 第29回 工場にAIを導入するメリット・デメリット、失敗するケースを解説2023.01.30 (Mon)
- 第34回 QCDとは? 生産管理の考え方やQCDの改善法について解説2023.01.30 (Mon)
- 第15回 工場の改善アイデア・事例5選! 業務改善を成功させるコツや実施手順も紹介2023.01.30 (Mon)
- 第17回 製造業のヒヤリハット事例5選 報告書の書き方や対策の進め方2023.01.30 (Mon)
- 第22回 製造業にIoTを導入するメリットとは? 事例や課題を解説2023.01.30 (Mon)
- 第24回 生産管理はAIでどう変わる? 製造業におけるAIの活用事例を紹介2023.01.30 (Mon)
- 第26回 工場は深刻な人手不足。その原因と5つの対策法とは2023.01.30 (Mon)
- 第39回 増えている製造業へのサイバー攻撃! 理由や対策法を徹底解説2023.02.15 (Wed)
- 第40回 工場の現場をペーパーレス化するメリットとは? 導入ステップやツールを紹介2023.02.15 (Wed)
- 第41回 多能工化とは何か? メリット・デメリットと失敗しない進め方を解説2023.02.15 (Wed)